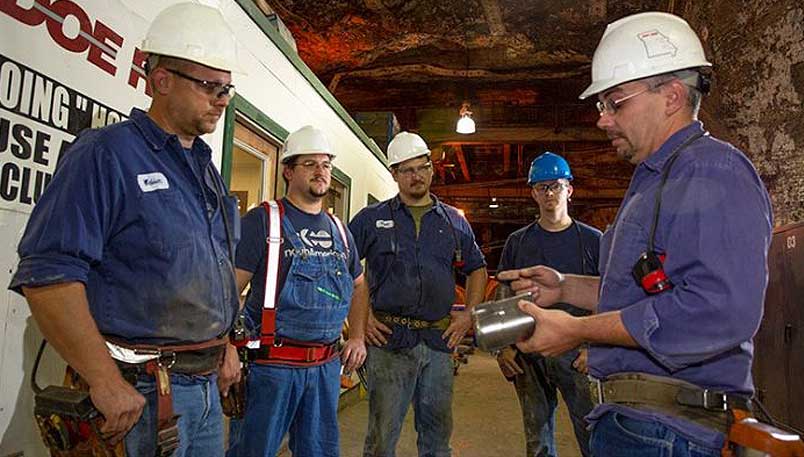
OSHA Safe + Sound Week is Time to Share Best Practices
Safety is always a top priority for the lead battery manufacturing and recycling industry. It’s demonstrated by members’ steadfast commitment to strict safety training. Now, as we celebrate OSHA’s Safe + Sound Week August 10–16, there’s a new dimension to safety: COVID-19 prevention.
The idea behind the annual event is to proactively identify and manage workplace hazards before they can cause injury or illness, while still improving sustainability and the bottom line. But what happens when you can’t see the hazard or know if a sinister threat like COVID-19 is present?
At a time when simple handwashing is as important to safety as steel-toe boots, everyone benefits by sharing best practices to stay safe in the workplace. This year, in addition to traditional safety successes, we’re sharing our experiences in coping with the global pandemic as the essential businesses of lead batteries continue to operate.
Factory Motor Parts (FMP): Boosting Employee and Community Safety
FMP prides itself on being a multi-generational, family owned company that provides premium original equipment and name brand automotive parts. The company is also a resource for independent service centers, dealerships, fleets and wholesale customers. As a supplier to the lead battery and recycling industry, the Eagan, Minnesota, company has more than 150 locations in 19 states.
Keeping Team Members Safe is #1.
Like other companies providing important services to keep the country running, FMP continues operations. According to Vice President Clay Johnson, “Our first concern is our team members. We want them to feel safe in the workplace, so we instituted flexible work schedules.” The company also provided protective gear and uses temperature scanners as employees arrive to work each day.
Retooling to Produce, Donate Household Cleaner.
To support the communities where they operate, FMP donated more than 15,000 gallons of SPLASH® (an FMP brand) household bleach cleaner to local public health organizations, such as firefighters, law enforcement, first responders, nonprofit entities and food pantries. The SPLASH facility also retooled one of its windshield wash production lines to produce additional product for donation. More than 1,100 organizations have benefited from this initiative, which Minnesota Governor Tim Walz recognized during a COVID-19 news briefing.
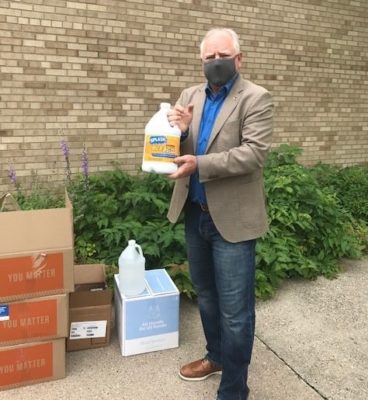
The Doe Run Company: Offering Incentives for Safety Program Participation
For more than 150 years, The Doe Run Company has been a company of innovators delivering a sustainable supply of select minerals, metals and services to meet the needs of a growing world population. Headquartered in Missouri, many of the company’s operations occur below ground, which adds an extra dimension of safety. In 2019, Doe Run employees completed approximately 15,000 hours of training, including extensive health and safety training. The company’s employees take an active role in recommending safety improvements across the company by participating in regular safety team meetings and completing ongoing training.
Near-Misses Program Offers $1,000 Grand Prize.
New safety initiatives, like the near-misses program at Doe Run’s Southeast Missouri Mining and Milling Division (SEMO), engage employees in flagging safety hazards, so they can be addressed before an incident occurs. Employees submitted more than 30 near-miss examples in 2019 and were entered in a quarterly drawing for a cash prize. One employee, a front-end loader operator, won the grand prize of $1,000 for submitting the most impactful near-miss of the year. The winning submission addressed how to safely locate, remove and store broken steel drill-rods to prevent them from becoming mixed in with ore piles.
Find it, Fix it Program Provides Monthly Opportunity for Employee Bonus.
Similarly, Doe Run’s Resource Recycling facility launched the new Find it, Fix it program to engage employees in hazard identification and promote proactive safety. Each month, employees identify and correct potential hazards. Employees have the opportunity to earn a bonus based on full participation. By proactively identifying and correcting hazards, employees become more aware of the hazards in their work areas, which helps strengthen the safety program and prevent potential injuries.
“At Doe Run, safety is more than a priority – it’s a value,” said Ryan Seelke, safety manager at Doe Run’s SEMO Division. “Priorities can change, but values are consistent. That’s why we hold frequent safety trainings, as well as find opportunities to talk about safety every day on the job. We watch out for each other, so every one of us can return home safely to our families each day.”
East Penn Manufacturing: Recognizing Safety Success Stories
From its facilities in Berks County, Pennsylvania, East Penn Manufacturing operates the largest single-site lead battery manufacturing facility in the world. The company is a perennial participant in the OSHA Safe + Sound Week program.
This year, East Penn will focus on recognizing the success stories of its employees related to instantaneous and ergonomic injury reduction, and proper hygiene. The latter is particularly important, said Troy Greiss, the company’s vice president of environmental health and safety (EHS) and regulatory affairs.
“COVID-19 has sharpened our already laser focus on employee safety. We’ve added temperature screening, social distancing practices, protective barriers, and new outdoor areas for employee breaks,” Greiss explained. “The hygiene practices our employees use for lead control fit well with those needed to prevent the COVID-19 spread, and we’ll keep adapting to stay at the forefront of prevention and overall best practices to help ensure a safe and healthy workplace.”
Training New Employees to be Safety Conscious.
East Penn’s safety committee members will also identify potential areas of overall safety improvement and help implement controls and preventative measures. The committee members will share this information, with a focus on employees new to the job, through one-on-one training, visual aids throughout the facility, and internal postings.
Gopher Resource: SafeStart Training Gives Company Head-Start on Pandemic Prevention
Last year, national lead battery recycler Gopher Resource launched SafeStart, a comprehensive, supplemental behavioral-based safety program that focuses on personal safety awareness and self-triggering on hazardous states/conditions. When COVID-19 hit, employees of the Minnesota-based company naturally applied their training to stay ahead of the crisis at facilities in Eagan, Minnesota, and Tampa, Florida, according to Jarret Vincent, the company’s vice president of safety and occupational health.
Responding Quickly and Aggressively to Crisis.
“Implementing SafeStart last year gave us a head start on how to handle COVID-19. Early on, we were prepared to respond quickly and aggressively with policies, some of which went above and beyond CDC guidelines,” Vincent said.
The company implemented advanced hygiene protocols for plant cleanliness, occupational health screenings, visitor lockdown, travel restrictions between campuses, and conducted an employee density study to determine physical distance measures. Within a week of COVID reaching the U.S., the company had shifted nearly one-third of its non-plant operations staff to work-from-home status. “Our speed and agility have been key in protecting our workforce,” Vincent said.
Implementing New Safety Technology.
As the pandemic continues, the company remains committed to new technologies, like wrist temperature scanners and sanitation foggers. Recently, the company began testing antimicrobial film on all high-touch handles and knobs. “I believe it is our duty as we learn more about COVID-19, to adapt to the best information and technology that we have at the time,” Vincent explained. While the company has had test-positive cases, Vincent said it has avoided wide-spread outbreaks, due to vigilant self-quarantine, contact tracing and testing.
“As a result of our background training with SafeStart, our robust policies and new technologies, Gopher Resource has helped keep its employees healthy and customer needs met during the global pandemic,” he concluded.
Crown Battery: Tapping a Competitive Safety Spirit
Crown Battery is a privately owned battery manufacturer based in Fremont, Ohio. The company emphasizes safety training throughout the year, and is always looking for new opportunities for people to learn – and to be sure that they are learning, especially COVID-19 prevention protocols.
A Chance to Learn and Earn.
Based on the success of its Safe + Sound week events last year, Crown Battery has implemented a similar program this year. It gives every employee a chance to learn and the potential to earn extra cash while doing so. Jim Anderson, Crown Battery’s health, safety, and environment manager, explained.
“The global pandemic has further reinforced safety as one of our core values. It’s an organization-wide effort.” He said that for Safe + Sound week, Crown wanted to create something a little different. “We want learning fun, and maybe even a little competitive.”
Completing Quizzes Increases Odds.
Crown developed a series of quizzes on safety topics ranging from Fall Protection and Forklift Safety, to Hazard Communication. As employees operate within the company’s facilities, they’ll see special Safe + Sound Week posters with QR codes that can be scanned with a mobile phone to access the quizzes. Each completed quiz with a passing score automatically enters the employee into a raffle for a gift card. Completing multiple quizzes earns additional entries into the prize pool.
Lead Battery Industry Soars in Safety Training
Though the pandemic is riddled with unknowns, members of the lead battery industry are well-poised to stay ahead of the crisis. Theirs is one of the most highly regulated industries in the U.S. for safety. Keeping workers “safe and sound” is an inherent part of what we do every day.