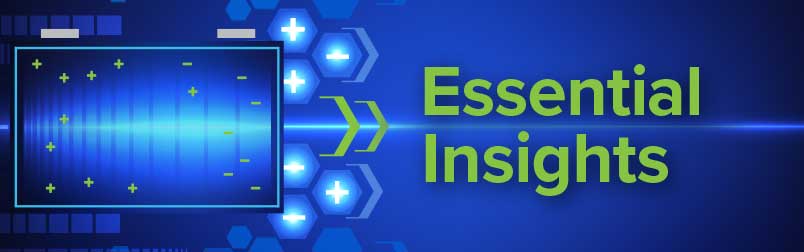
In a recent article published by Innovation News Network (INN), Roger Miksad, President of Battery Council International, explains how the path to sustainability will need to include existing battery recycling as well as the development of policies and processes for additional battery chemistries. INN is a go-to source for the latest news dedicated to research, emerging science, policy and innovation topics across the globe. This article is reprinted from INN online with permission, copyright 2024. Note: Because INN is published in the U.K., some words may use the British spelling.
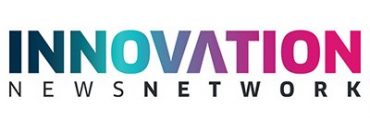
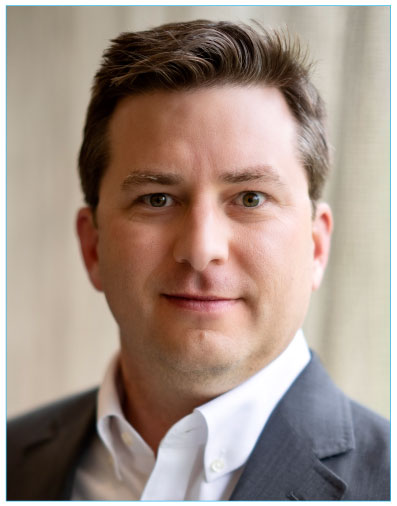
The United States is experiencing a battery-powered revolution in transportation and grid energy storage that promises enormous environmental and economic gains. Lithium-ion, advanced lead-acid, flow, sodium-ion, and emerging battery chemistries have enabled the rise of electric vehicles (EVs) and are supercharging the transition to renewable energy sources. Continued innovation promises even greater capabilities.
But with any revolution comes disruption and risk. As usage explodes, we must ensure this battery boom does not translate into a battery waste crisis.
Fortunately, the road to safer and more sustainable battery lifecycles has already been paved by the nation’s most recycled product: The stalwart lead battery. The lead battery industry operates an unparalleled collection and recycling system. For over 30 years, lead batteries have been recycled at a nearly perfect 99% rate, far outpacing any other consumer product, according to a recent recycling rate study.
This was not by accident but rather through purposeful policies and industry commitment to circularity. Lead battery recycling diverts hundreds of millions of pounds of lead and plastic from landfills annually and supplies roughly 90% of all lead used domestically for new battery production.
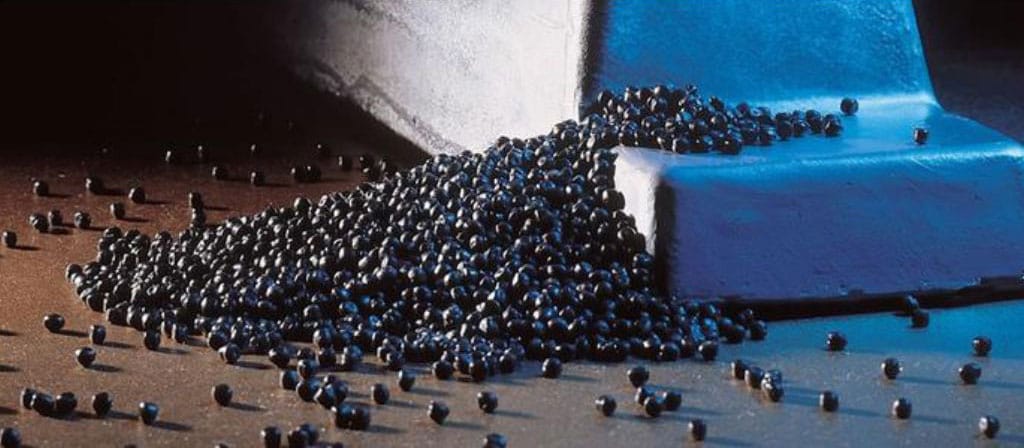
Other battery industries should embrace and replicate lead battery recycling’s core strategies of consistent labelling standards, widespread free consumer collection opportunities, prohibitions on improper disposal, and industry-funded transportation and processing networks.
Adopting these policies broadly across lithium-ion and other emerging battery chemistries is essential to continued innovation. It will ensure sustainable growth of a robust domestic battery manufacturing and recycling industry rather than trading one environmental challenge for another.
Building Battery Recycling into the Foundation
The lead battery industry’s recycling achievements trace directly back to forward-looking policies pursued by the industry starting in the late 1980s. Businesses recognised recycling would need to be designed into our products, manufacturing processes and collection channels – not bolted on after the fact.
With encouragement from the U.S. Environmental Protection Agency (EPA) and environmental groups, battery manufacturers and recyclers found consensus on legislation that ensured collection opportunities were available wherever batteries were sold. Within a decade, nearly 40 states representing over 80% of the population enacted laws embracing these core principles:
- Ban improper disposal in landfills to prevent releases;
- Require all battery retailers also accept returns from consumers;
- Mandate that manufacturers arrange for transportation and recycling; and
- Incentivise consumer returns through refundable core charge deposits.
These simple but purposeful policies completely reshaped consumer collection channels and recycling efficiency. Within a few short years, lead battery recycling rates jumped from below 80% to consistently above 99%.
The enactment of these forward-leaning policies positioned the lead battery industry to simultaneously expand domestic manufacturing and increase the use of recycled materials. Today’s robust recycling network supplies more than 85% of lead metal demand for new US battery production and powers a $33bn* industry supporting 121,000* jobs, according to a recent economic impact report. (*2021 data)
Supporting Safe Collection of all Chemistries
With today’s diversity of battery chemistries serving vastly different applications, uniformly imposing rigid legislative mandates risks unintended consequences. We must take care to avoid disrupting what works – like lead battery recycling – while thoughtfully extending proven policies to emerging chemistries.
Lithium-ion batteries help power devices and technologies previously unimaginable but pose fire and safety risks if mishandled, especially during recycling. As usage soars over the next decade, inadequate sorting and recycling infrastructure threatens contamination of existing lead battery streams. Such cross-contamination can decrease process efficiencies, compromise the quality and safety of recovered materials, and endanger collection workers.
A key component of the safe and profitable operation of any metals recycling operation is efficiency and consistent throughput. Battery Council International’s recycling members process more than 160 million batteries per year for recycling across North America, with hundreds of millions more processed around the world. Across the major recycling facilities in the US, a typical battery recycling facility can process 80 or more vehicle batteries per minute.
The lead battery recycling process is a highly specialised process honed over the decades to be highly efficient when there is a steady and clean supply of used batteries. This efficiency is one of the core drivers of lead batteries’ unparalleled recycling success. However, when incompatible materials, such as lithium batteries, enter the lead battery recycling stream, they can reduce the quality of the recovered materials.
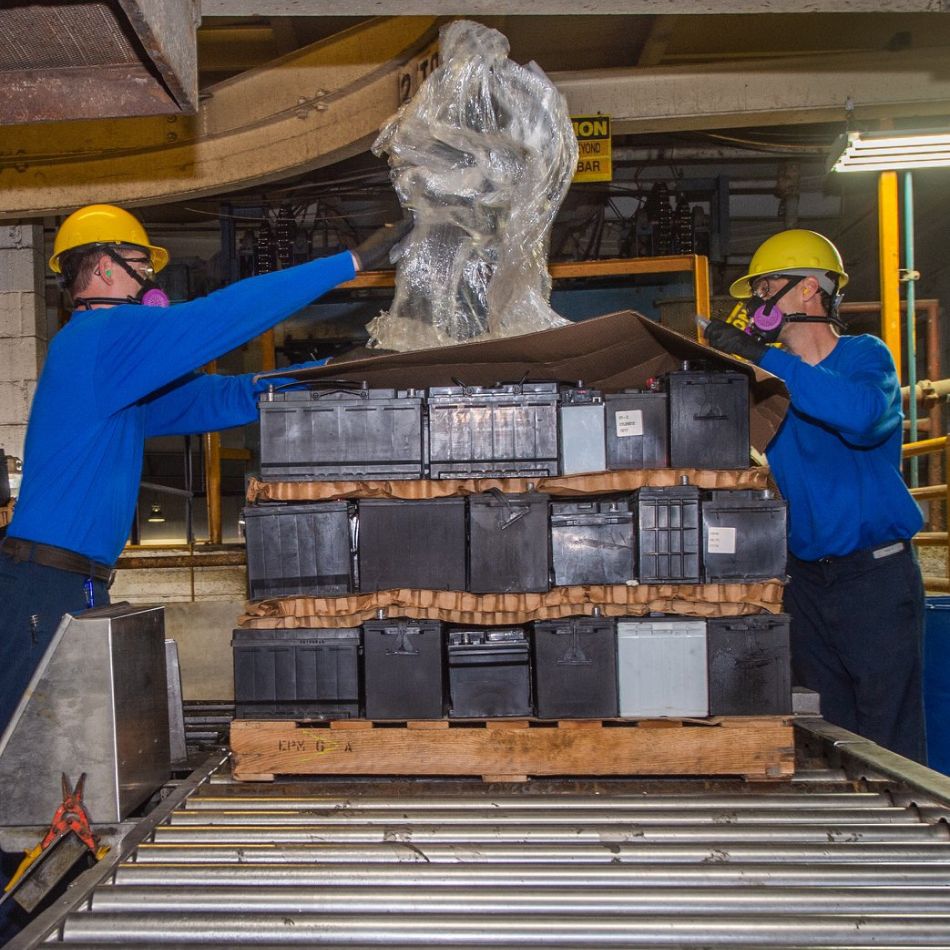
Most importantly, contamination of the lead battery recycling stream poses a serious threat to employee safety. Lithium batteries dramatically increase the risks of fire and explosion posed to facilities and workers if they inadvertently find their way into the lead recycling process. This is, in large part, due to the high energy potential of these batteries combined with their relatively low tolerance for physical damage, such as the crushing that has long been a part of the proven lead recycling process.
Every lead battery recycler with whom BCI works catches multiple lithium batteries every day, and all have experienced unfortunate incidents when lithium batteries slipped through the rigorous inspection processes.
The sorting and identification process is becoming ever more difficult as more lithium batteries are designed to mimic lead batteries, and volumes are increasing. Our members remain vigilant about their recycling streams and, in the event of lithium contamination, can often successfully mitigate any negative effects. But no facility can solve this challenge alone; it’s up to public officials and private sector participants to work together to ensure everyone is doing their part to protect public health and safety.
Further complicating matters, the introduction of additional ‘ride-along’ contaminants requires the recycler to perform additional time-consuming and expensive metallurgical refining steps to achieve the necessary quality of recovered metal. This increases the carbon emissions and energy consumption of the process and increases the amount of waste by-products produced by the process.
The 99% recycling rate of lead batteries is a huge point of pride for our industry, and we want to ensure the broader disposal and recycling infrastructures for other battery chemistries do not undercut the sustainable model we have built over the decades.
The experience of lead battery recyclers is not unique. The contamination of any recycling input stream with incompatible or potentially dangerous materials creates real challenges to the quality of the recovered materials, the positive environmental impact, and the participation rate among businesses and consumers across the supply chain.
Efficient and safe recycling processes are good for everyone. That’s something we’ve learned firsthand in the lead battery industry, and we’re eager to help apply our lessons learned to other areas.
Battery Chemistry Labelling Standards and Guidelines are Needed
Protecting America’s current and future recycling infrastructure requires consistent and standardised labelling to enable proper identification and sorting between distinct chemistries and applications. BCI supports the adoption of clear, human-readable sorting labels on all batteries—ideally embracing a globally standardised format. Existing voluntary standards such as IEC 62902 can provide a foundation for industry, government, and NGOs to establish labelling schemes.
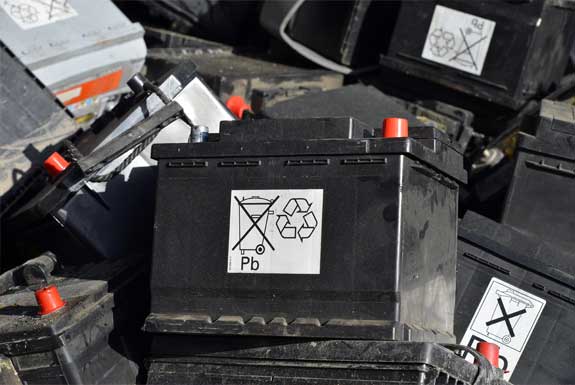
Currently, there is no mandate in the US for all battery chemistries to use a uniform human-readable identification for battery chemistry. This has created problems in the marketplace because batteries of similar size can be readily confused and are frequently placed into the wrong recycling collection stream. EPA should consider how best to ensure that consumers and collection network participants have the information needed and the opportunity to direct each type of battery to the right collection stream.
Battery labels should have a consistent and simple marking (e.g., a colour-coded, three-chasing arrows loop) across all battery chemistries to encourage and aid recycling. At a minimum, recycling and chemistry markings should address three primary goals. In order of priority, they are:
- Instructing consumers to keep batteries out of the trash and curbside recycling, and are directed to dedicated battery recycling networks where available;
- Providing consumers and recycling network employees with human-readable information to enable the sorting of used batteries among major chemistry families (e.g. Pb, Li-ion, Ni-Cd, Ni-MH, and Li-metal); and
- If appropriate within a chemistry family, inform recyclers of the unique features, components, and/or constituents of the batteries for recovery (e.g. cathode material).
As battery labelling standards are adopted, it is important those standards be consistent across chemistries sold on the US market, regardless of the country of origin. Requirements imposed only on domestic manufacturers will fail to address the problem considering the dominance of foreign manufacturers of lithium and other battery chemistries. Labelling standards must be identifiable and enforceable by US Customs Inspection officials to ensure that batteries entering the US market are compliant and do not pose additional hazards.
Battery labelling best practices should also consider, in addition to a recycling and chemistry disclosure marking, additional safety and hazard information to inform users and recyclers of necessary storage requirements, fire hazards, and other information. OSHA and CPSC labelling regulations provide ample guidance and foundation.
Labelling is not a panacea, however, and even reliable labelling cannot eliminate risks entirely without additional safeguards built into collection and transportation channels. All participants in the collection and return chain must be trained in the proper sorting and segregation of chemistries and in the safe handling and transportation of used batteries.
Closing the Loop Through Circularity
With sound policies and industry initiative, we can replicate the circularity success of lead batteries across additional chemistries. However, the unique residual value of recyclable lead components may not directly transfer to other battery types.
Most lithium-ion recycling is unprofitable today, without subsidies or processing fees. Achieving true circularity requires continued technological innovation to improve economics. Industry must collaborate with regulators in pursuing pragmatic advancement of both recycling and collection infrastructure. With patience and purpose, commercially viable recycling pathways can be developed for emerging applications.
The alternative is simply unacceptable: Deepening and growing the known environmental and safety threats. We must, therefore, learn from the proven lead battery industry playbook to enable safe battery disposal across the energy storage landscape.
A battery waste crisis is not inevitable. Averting it requires intentional action, beginning today. With foresight now towards sustainable collection and economically viable reprocessing, our clean energy future remains a path towards circularity.