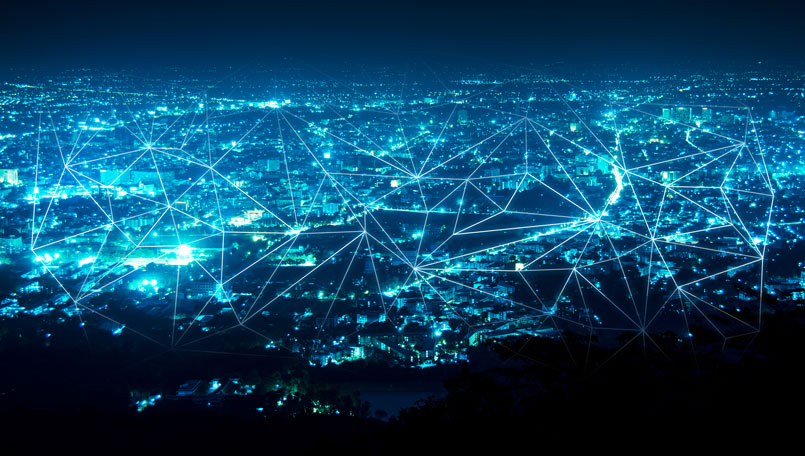
The Need Is Great. The Pressure Is On.
The world is under intense pressure to dramatically expand energy storage. To give a sense of the terrain ahead – and progress underway – Essential Energy Everyday has summarized “The Future of Energy Storage” webinar.
It was presented by the U.S. Department of Energy’s (DOE) Argonne National Laboratory on November 19. The event is part of a series that focusses on using science to improve materials management.
Setting the Stage for Webinar Presenters
As COVID-19 has proven, domestic sources of energy and energy storage are critical. They ensure national security, energy resilience and a reliable manufacturing supply chain. With a keen focus on innovation, DOE and its National Laboratories are partnering with private industry to solve the immediate challenge of scaling energy storage to meet the world’s rapid pursuit of:
- Electrification
- The deployment of low-cost renewable power sources
- Greater use of electronics and technology
- Mitigating climate change
Dr. Srinivasan, Argonne National Laboratory: U.S. Has Strong Energy Storage Ecosystem
Webinar host Dr. Venkat Srinivasan facilitated presentations by several top experts (see participant bios). Dr. Srinivasan is director of the Argonne Collaborative Center for Energy Storage Science, a leader in the search for solutions to expanding energy storage. He is also deputy director of DOE’s Joint Center for Energy Storage Research.
As he introduced the speakers, Dr. Srinivasan noted, “We are currently in a race to discover and manufacture batteries of the future,” and that is taking place in Asia, Europe and the U.S.
He said the Asian economy has had a significant head start. In light of this worldwide competition, he questioned how the U.S. can compete, especially since the transition from lab to market is not easy or inexpensive.
Also, there are many supply chain aspects to consider, such as where materials are sourced, their availability, performance, and if they can be recycled. But the forecast is bright, according to Dr. Srinivasan.
“We have fantastic news. The U.S. has a very strong ecosystem around energy storage … lots of universities, national labs and industry are [working to solve this problem].” And, he added, “The federal government is stepping up in a big way” by forming consortiums to develop advanced batteries.
Dr. Willy Shah, Harvard: Meeting the Challenge
During his presentation, Dr. Willy Shah, a professor at Harvard’s Business School focused on what he called an economic imperative for growth – a once-in-our-generation opportunity to meet the challenge of developing U.S.-based energy storage.
“One of the things I’ve been advocating for is energy storage, like for grid modernization. If I think about the global environment on trade and the after effects of the pandemic, we have economic disruption, economic nationalism and the need for stimulus and the willingness to spend a lot of money. There’s a real opportunity to get the country behind energy storage if we can pick goals that people understand.”
Vineet Mehta, Tesla: Transportation’s Breathtaking Need
Vineet Mehta is the director of battery technology and powertrain architecture and modeling at electric vehicle manufacturer Tesla. He provided an eye-opening gauge of the need for energy storage.
“If we make all transportation electric, the scale of the problem is 100x growth, and that’s just for road transportation without touching on other types.” He said we can’t scale fast enough if we follow our current plan.
Part of the challenge for lithium-ion batteries used in Teslas is that the current supply chain is diffused and “spread all over the planet.” In addition to the energy and cost of purchasing materials, there is a cost in the cumulative miles required to bring the materials to one place for manufacturing. To meet the need for stationary storage, Mehta said you need 135 giga factories, $2 trillion in capital and 2.8 million people.
Joe Cresko, DOE: The Roadmap to Improve Supply Chains
Joe Cresko is chief engineer at DOE’s Advanced Manufacturing Office. He outlined the need to improve critical material resiliency in supply chains and listed three of DOE’s goals to do so:
- Diversify the supply chain for critical materials, including domestic production and processing
- Develop element, material and/or system substitutes to reduce dependence
- Drive recycling, reuse and more efficient use of critical materials.
This crosscuts with the DOE Energy Storage Grand Challenge to create a comprehensive program to accelerate the development, commercialization and use of next-generation energy storage technologies that also sustain U.S. global leadership in global storage.
Dr. Tim Ellis, RSR Technologies: A Scalable, Domestic Supply Chain Is Ready
The program closed with Dr. Tim Ellis, president of RSR Technologies. RSR is the research development arm of Ecobat, the world’s largest lead recycler, recycling nearly 900,000 tons of lead annually in three continents.
Dr. Ellis spoke of the requirement for more R&D to meet the vast energy storage need and to reduce the cost per KWh of lead batteries to DOE’s target of $35. That would make them the most cost-effective energy storage source. While previous speakers spoke of new and emerging battery chemistries, Dr. Ellis explained that lead battery manufacturing and recycling is already established with a long history of reliability. He offered these numbers:
- The domestic manufacturing and recycling of lead batteries is a $26.3 billion U.S. industry.
- It supplies more than 90% of the demand for North American lead batteries.
- The use of recycled lead required 90% less energy and produces 90% less greenhouse gases compared to virgin ore mining.
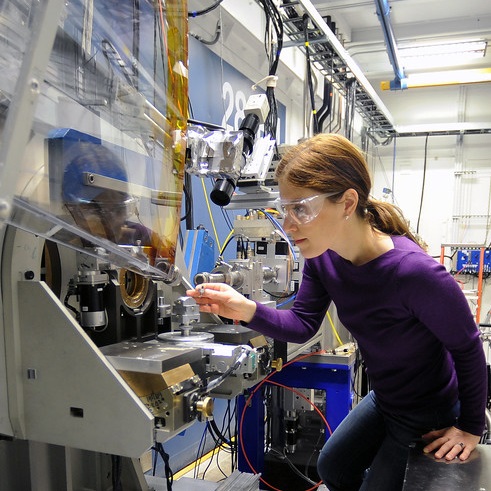
Advancing Lead Battery Performance is Underway
To advance the performance of 160-year-old lead battery technology, the lead battery industry has formed a consortium called the Lead Battery Science Research Program (LBSRP). They are working with scientists at Argonne National Laboratory to research the unknown properties of lead to advance battery performance.
Dr. Ellis reiterated that for lead to remain competitive, it needs to meet all the attributes for modern energy storage at a price of $35 per kWh. The question is, how?
“We [lead batteries] already have domestic manufacturing that’s large and robust. We also have a total closed-loop circular economy, with our recycling.” Dr. Ellis contrasted that with lithium-ion batteries. “I prefer to call it demanufacturing. These batteries aren’t coming out as nice cubed cells. They’re coming out as complex systems that have to be unmade and, oftentimes, they’re not made to be unmade. This slows down the ability to recycle and do it as an economically viable price point.”
Lead Battery Research Focus Areas
Dr. Ellis identified three research areas of the LBSRP that align with DOE’s expertise and facilities.
- Product architecture. “The basic design of a lead battery has remained constant for almost 100 years. We have flat plates, we have material on those plates, and we assemble those batteries. To increase the efficiency … we want to remove the lead that isn’t being useful for the performance of the battery.”
- Materials utilization. “This is probably the most important one for us to hit that $35 kWh metric. Right now, the average lead battery is only using about 40% of its active material. We can hit $35 per kWh by just increasing that to 70%, and that’s been a huge effort by the industry. We’re working with Argonne and some of the other national laboratories.”
- Control technology. “What we’re looking at now is how we can treat lead the way it wants to be treated through advanced controls technology, which allows us to maximize the opportunity of lead batteries to improve performance.”
The consortium uses Argonne’s Advanced Photon Source, recognized as one of the world’s brightest x-ray machines. “We’re able to look inside a lead battery as it’s operating … and understand the locations of the active material. This is huge.”
He also said that to improve the performance along with the price, lead batteries have to charge faster and cycle more. “Once we’ve got that, the question is how to … modify the additives or chemical structure of the battery.”
Watch the Webinar
To watch “The Future of Energy Storage” webinar, click here. And, we encourage you to click below to learn how innovative lead batteries are already one solution to the future of energy storage.