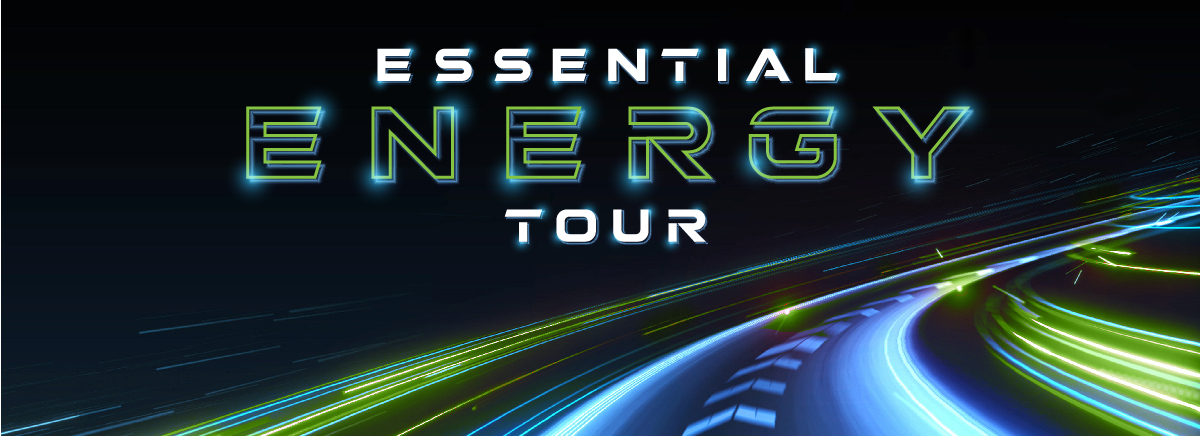
We’re virtually touring several U.S.-based manufacturing and recycling stars who help form the strong network of BCI member companies. They provide batteries and the services and supplies that are used to create those batteries. They also comprise the vast domestic infrastructure that ensures a reliable energy source exists to power the U.S. economy.
Lead Battery Recycler Plays Critical Role in Success of Domestic Circular Economy
Recycling lead batteries is a cornerstone of the successful circular economy of lead batteries. They are designed to be infinitely recycled and, in turn, supply a reliable stream of materials for reuse. Minnesota-based Gopher Resource is an environmental solutions provider and a key contributor of recycled materials used in domestic manufacturing.
Annually, Gopher Resource sustainably recycles millions of automotive, stationary and industrial lead batteries. In total, the company keeps more than 26 million spent lead batteries from landfills every year. Gopher Resource safely recycles the batteries’ lead and plastic into valuable raw materials from two campuses, one in Eagan, Minnesota, the other in Tampa, Florida. The Minnesota site also includes the subsidiary company, Resource Plastics.
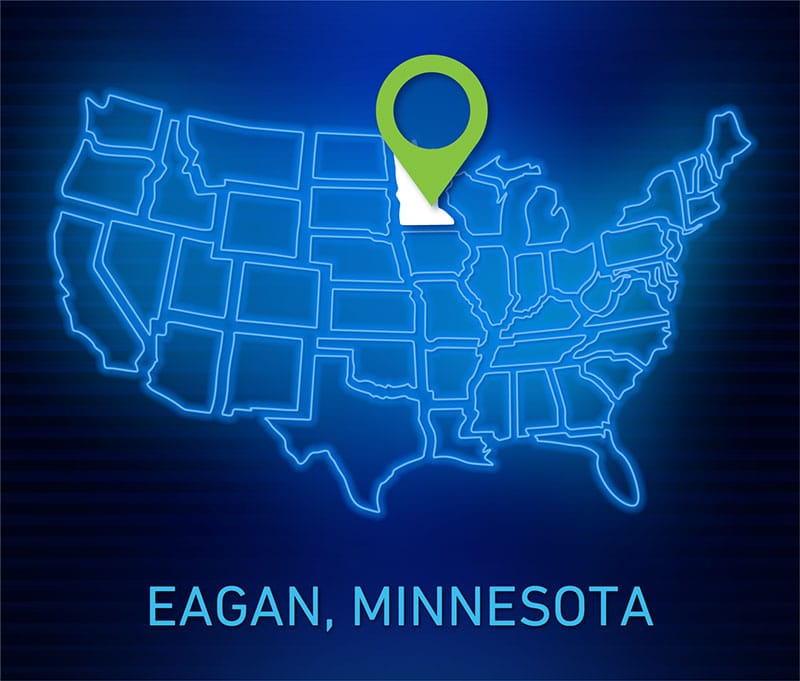
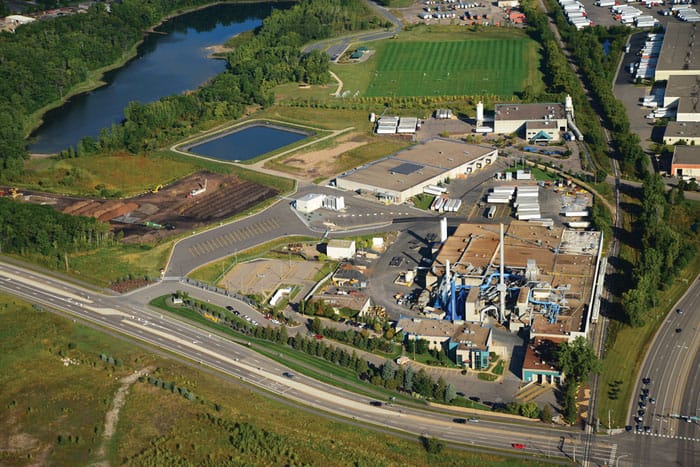
Key to a Domestically-Driven, Circular Economy
The lead battery industry has created a closed-loop circular economy that has become the model for other battery chemistries to emulate. This commitment to responsibly source, use, reuse and manage materials has resulted in a nearly 100% domestic recycling rate. Likewise, a typical new lead battery is comprised of over 80% recycled material, including lead, acid and plastic sourced from companies like Gopher Resource. Annually, Gopher Resource processes nearly 600 million pounds of lead for reuse, nearly 40 million pounds of polypropylene (plastic) into pellets for reuse, and numerous specialty alloys.
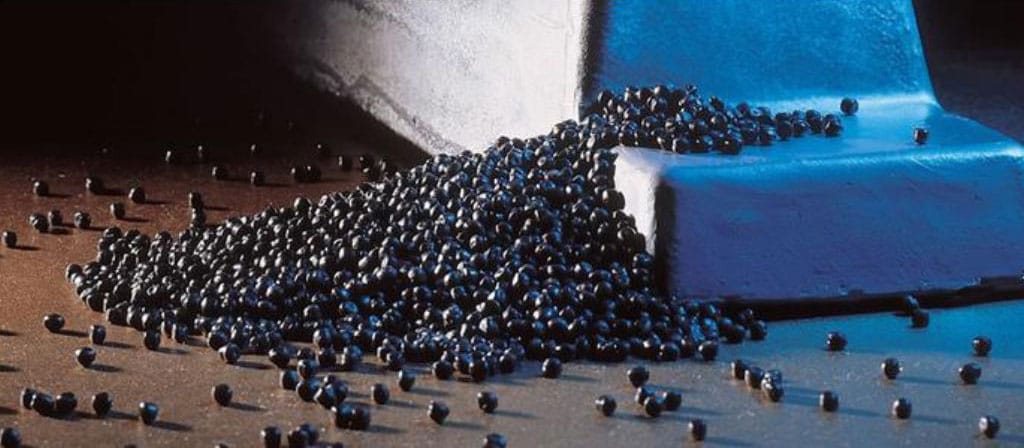
Continuous Innovation Supports Clean Energy Future
Throughout its 75-plus years in business, Gopher Resource has made proactive investment in innovation and research to help meet the nation’s rapidly growing demand for energy storage.
Brian Leen, president and CEO of Gopher Resource, said, “The important work by our R&D team is a critical component in the country’s energy future. Advances in the safety, productivity and sustainability of the recycling process are important for our environment, industry and our customers.”
Here are examples of how Gopher Resource is working to advance innovation and safety, and improve the closed-loop processes for the industry:
- A new 3,000 sq. ft. R&D lab in Eagan to advance next-generation recycling solutions.
- Development of an innovative process to address waste valorization and reduce their solid waste stream to landfills by up to 99%.
- Investing millions of dollars in sustainability projects, like stormwater collection and reuse distribution systems.
- Participating in government-funded research to support energy innovation and advance recycling efficiency.
- Industry partner for the Material Recovery Technologies for Defense Supply Resiliency (MRT-DSR) initiative funded by the Department of Defense (DOD) to advanced recovery and recycling technologies of critical minerals and materials.
- Supporting lead battery research initiatives in energy storage and automotive applications as a member of Consortium for Battery Innovation (CBI).
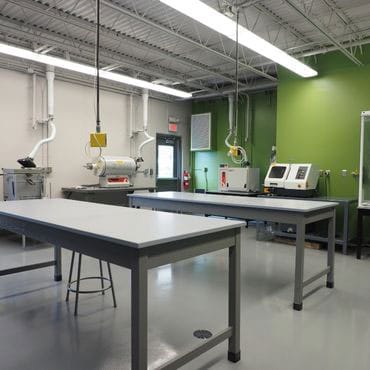
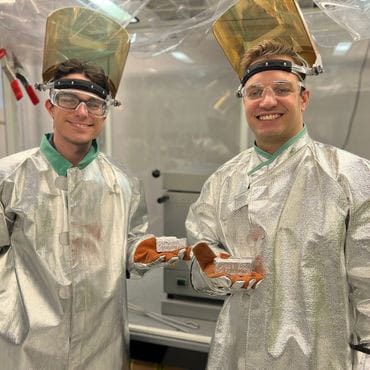
- Since acquiring its Tampa facility in 2006, investing over $230 million to upgrade and advance the facility (almost half to maintaining employee health and safety, and environmental protection).
Essential Environmental Work – and Workers
Gopher Resource provides over 600 green jobs within a unique, yet highly necessary, industry. There are only ten lead battery recycling facilities in the U.S.; Gopher Resource operates two, which collectively keep 130 million used lead batteries from landfills each year.
Company President and CEO Leen is passionate about conveying how critical the company’s environmental services and employees are, as well as their focus on safety and sustainability.
“We use the latest technologies and standards to transform lead batteries and other lead-bearing materials into reusable resources,” Leen explained. “By recycling, we’re keeping potentially hazardous materials out of landfills and saving valuable resources that domestic manufacturers need.”
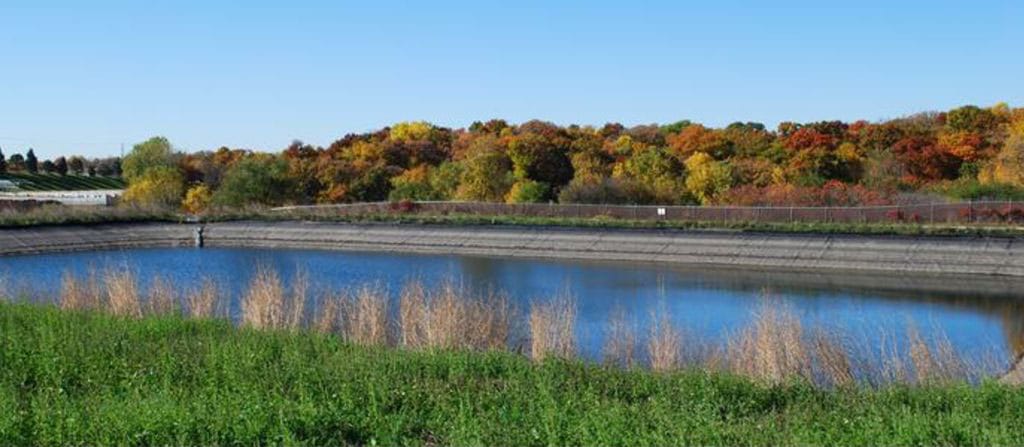
Building Strong Communities
Gopher Resource knows that good things happen in strong communities. The company and its employees give generously to support the communities in which they live. That includes participating in local, state, national and global initiatives and supporting environmental stewardship.
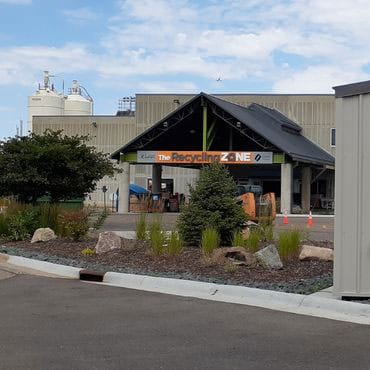
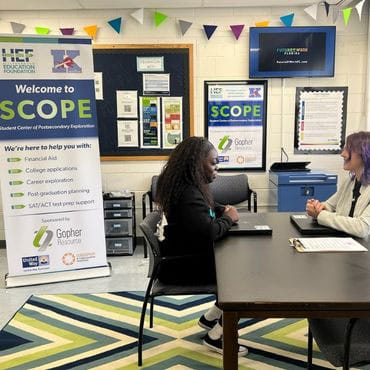
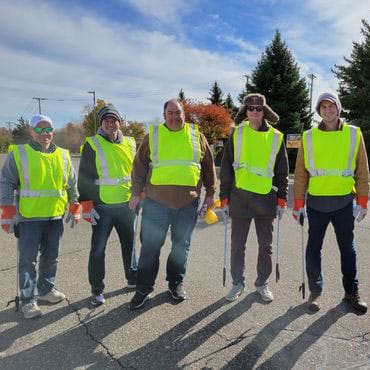
For example, the Eagan campus operates The Recycling Zone in Dakota County, Minnesota’s second-largest community recycling and education center collecting household hazardous waste and recyclables. The Tampa campus recently helped launch SCOPE (Student Center of Postsecondary Exploration), which provides one-on-one college and career planning within King High School in Tampa.
Thank you, Gopher Resource, for letting us get to know you better!
Watch this space for other tour stops, as we travel the country sharing details about an industry that provides 60% of the world’s rechargeable energy storage and contributes billions of dollars to our domestic economy. Until then, read about Tour Stop #1 with Hammond Group, Inc. and Stop #2 with Crown Battery.