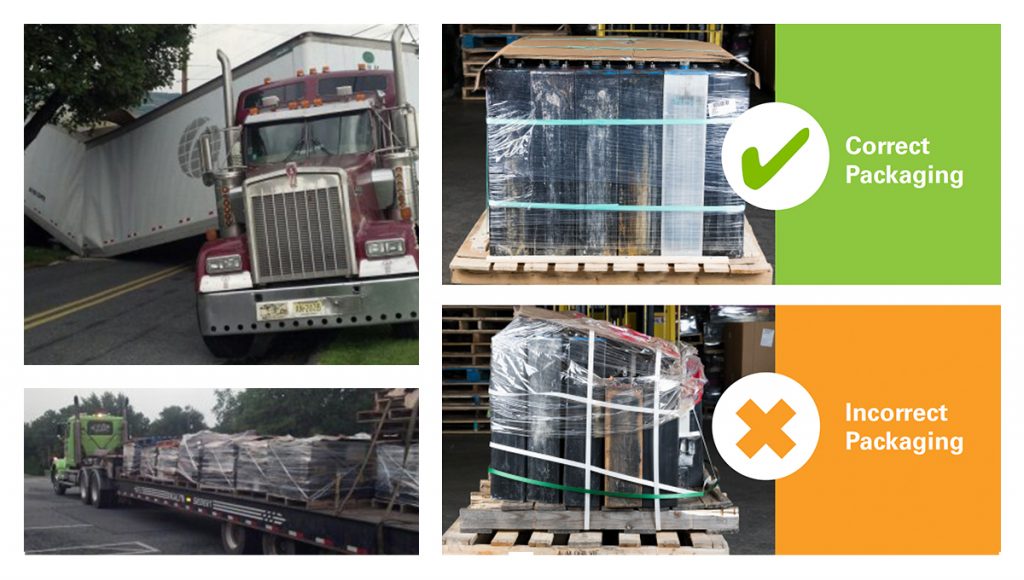
This is the last post in our three-part blog series during this important week.
As we finish our posts for Safe + Sound Week 2018, we don’t want to overlook that lead battery manufacturers, recyclers and suppliers – though competitors in the marketplace – are united to promote safety locally, nationally and internationally.
Here’s a prime example. The industry is working together to create awareness of the risks that occur to workers and facilities when 1) lithium batteries are mixed with lead batteries for recycling, 2) lithium batteries are improperly disposed of at waste facilities, and 3) any battery heading for recycling is improperly packaged.
Why Lithium is a Problem
Lead batteries are 100 percent recyclable; lithium batteries are not, and they must not mix with the lead battery waste stream. When lithium batteries are crushed during the lead battery recycling process, they can explode, potentially causing injury or even death.
This is so problematic, that Call2Recyle, a nonprofit public service organization, has launched a safety campaign to educate Californians on battery safety and recycling. The organization’s research revealed that in 2017, 65 percent of fires reported by 26 waste facilities throughout California were said to have been caused by batteries.
Crown Battery, who funded an educational video for the industry on the topic of safe recycling, is studying and testing the benefits and drawbacks of lithium ion. The company’s CEO, Hal Hawk, gave this rationale for supporting – and sharing – the video: “One thing no one can argue is the volatility of the chemistry [lithium] in use, depending upon applications, and in the recycle stream. Lithium and the lead acid recycle process do not mix, and when lithium batteries inadvertently enter the lead recycling process, the result is catastrophic.”
Proper Packaging Critical, Too
Batteries must also be packaged properly for transport. Interstate Batteries Recycling has created Green Standard packaging procedures, a strict, self-imposed battery handling and recycling process. It allows for on-site inspection for leaking battery cores, special packaging procedures, and a battery bag that will contain any leakage from a cracked or broken auto battery
Tod Lyons, Interstate’s communications and sustainability manager, said, “We have trained some of the largest scrap companies and environmental companies in the country on how to properly package lead batteries for transport.” The company will soon launch training videos on battery packaging. Viewers can receive a packaging and handling training certificate after answering embedded quizzes within the videos.
Companies Share Educational Efforts
Other companies have also created materials to assist in training across industry and company lines.
Interstate Batteries Recycling, Gopher Resource and East Penn Manufacturing have all created training materials to use within their companies and to share throughout the supplier chain. The materials highlight the need to safely identify and separate lithium batteries from the recycling stream.
For example, Gopher Resource recently shared with their business partners, suppliers, brokers and collection sites a pictorial Battery Identification Guide. It’s the culmination of more than a year’s worth of collecting and photographing samples of conforming and non-conforming materials and batteries. The guide includes automotive-type batteries; industrial and steel case batteries; gel cell, standby, backup and telecom batteries, and other lead-bearing materials. The company also created a series of posters, made freely available to others in the industry.
Safety Has International Reach
The safe handling of lithium batteries isn’t limited to the U.S. battery industry. It has worked with the International Electrotechnical Commission (IEC), a global standardization body, to create a global identification system to distinguish lithium and other rechargeable batteries from lead for the purpose of recycling. The system includes color coding for labels and/or the casing or sleeve of the battery components. The process was begun years ago and passed last April.
Safety Always
While Safe + Sound Week as an event ends August 19, being safe remains a focus for the lead battery industry – who lives the mantra of “Everyone Going Home Safe and Healthy Every Day.” – year round.
Access our first two blogs in this series, “Safe + Sound Week: Employee Safety” and “Safe + Sound Week: Safe for Our Communities and Environment.