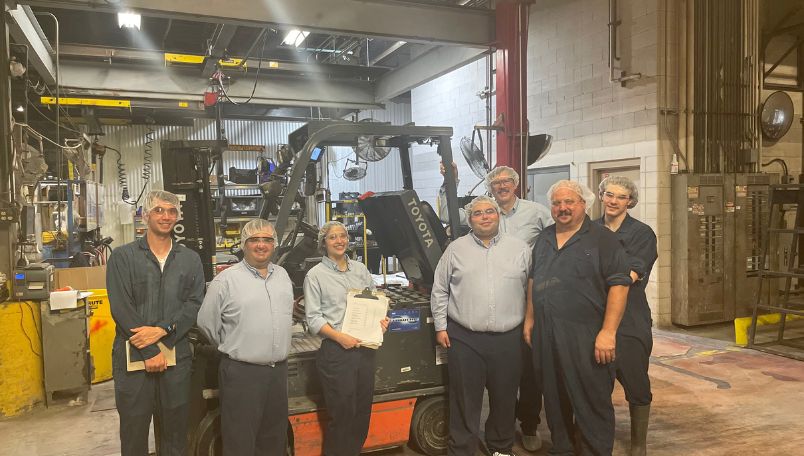
The Stryten Energy finishing department employees conduct an audit of the plant’s forklifts, which includes checking the proper functionality of the truck and the water levels in the Stryten Energy Tubular LMX battery in Kansas City, Kansas.
Working Safely Throughout the Year
Safety is a priority in any workplace, but it’s taken especially seriously in a manufacturing facility. The work environment is quite different from that of an office worker – while both may enjoy an open floor plan and ergonomic equipment, plant workers also encounter robotics and heavy machinery. A casual Friday on their job may still require personal protection equipment as part of their work “wardrobe.”
Looking out for both workers in the office, and on the manufacturing floor, is the U.S. Department of Labor’s Occupational Safety and Health Administration (OSHA). Established by Congress in 1970, OSHA’s goal is to ensure safe and healthful working conditions for workers by setting and enforcing standards and by providing training, outreach, education and assistance.
A key hallmark of the department is its annual Safe + Sound Week held each August which recognizes the successes of workplace health and safety programs and offers information and ideas on how to keep American workers safe. Simply stated, everyone deserves to go home safe each day.
This saying is a value embraced by lead battery manufacturing and recycling companies. With nearly 26,000 employees across the U.S., companies in the lead battery industry take safety seriously. This is the first of three blog posts describing the safety culture of lead battery manufacturing facilities who are members of Battery Council International.
Protecting the Industrial Athlete: The Importance of Safety in Manufacturing
Safety in manufacturing environments is a top priority year-round for industrial workers. And for Stryten Energy, safety is a core value. Much like professional athletes, “industrial athletes” can take important steps to protect their health and safety, as well as that of their teammates.
Self-Care is Part of Safety
Safety in manufacturing includes self-care. It takes time to acclimate to a hot manufacturing environment, and even then, heat-related illnesses are a considerable risk. It is crucial for industrial athletes to stay hydrated on and off the job and to take heat breaks if necessary. Drinking plenty of water and electrolytes or resting in a cool room can make a big difference while at work. It is important to remember the 2:1 ratio of water to electrolyte drinks. For every one cup of sports drink or electrolyte beverage, drink two cups of water to ensure the proper balance of sodium and potassium.
If industrial athletes are dehydrated, they might experience decreased physical performance or cognitive impairment, which could lead to serious safety risks in the workplace. Just a 2% water loss can cause a decrease in physical performance, and even mild dehydration can disrupt cognitive function.
Industrial athletes can also help ensure their safety at work by getting an adequate amount of sleep. Sleep deprivation of 18 hours is equivalent to a blood alcohol level of 0.05%. Going without sleep for 24 hours equates to a blood alcohol level of 0.10% – higher than the legal limit in all 50 states.
A worker who is dehydrated or sleep-deprived might experience decreased coordination and reaction time, as well as diminished judgment and reduced cognitive ability. Impairment not only puts the individual worker’s health and safety at risk, but it could also endanger others. Thus, self-care is a critical component for safety in manufacturing.
Personal Safety on the Job
Once industrial athletes are on the job, they follow all required safety rules. The most important safety in manufacturing rule, one where workers have the most control, is wearing proper personal protective equipment (PPE). Much like a professional football player would never consider walking onto the field without his helmet and shoulder pads, the industrial athlete should never walk onto the manufacturing floor without eye and ear protection. In some instances, additional PPE, such as coveralls or a specialized uniform, respirator, or gloves, may be necessary. Routine hand washing is also a must for anyone on the plant floor, as well as for general well-being.
Situational awareness is yet another safety tool for industrial athletes. They are aware of moving equipment, such as forklifts, where team members are standing in relation to heavy machinery, and other potential hazards on the plant floor. They always know where eyewash stations and fire extinguishers are located and are able to identify the building exits in case of emergency.
In addition, it is critical to be aware of other teammates and have an understanding of their roles. All members of a NASCAR team have clearly defined roles and responsibilities, and each one is key to the success of the team. Workers in manufacturing situations are no different. Everyone on the team has an important role to play in order for the operation to run safely and smoothly.
Safety Is Everyone’s Responsibility
Safety in manufacturing is clearly a team goal, and team members can protect one another by being alert for warning signs and at-risk behaviors in others. Each worker has the right to a safe working environment. All industrial athletes should feel empowered and are encouraged to speak up, without fear of reprisal, if a situation is not safe or if someone on the team is not following proper safety protocols.
Safety rules are not implemented and enforced to make workers’ lives difficult. In fact, it’s just the opposite. Safety rules and regulations provide an environment that allows industrial athletes to focus on their work, so they can safely return home to their families at the end of each day.
Authored by Jennifer Meglic, Director Health & Safety Operations at Stryten Energy, and reprinted with permission from Stryten Energy, a leading provider of energy storage solutions for transportation and industrial markets headquartered in Alpharetta, Georgia.