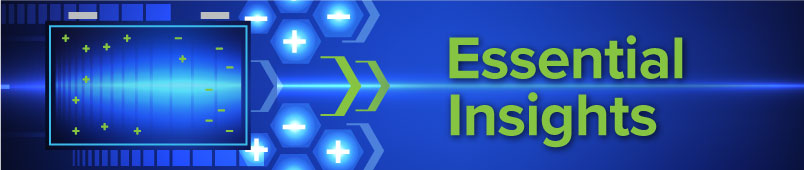
Our guest blogger is Terry Murphy, president, CEO and chairman of Hammond Group. Terry started working at Hammond in 1975 with a summer job, joining his father who was the Hammond Plant Manager, then went on to graduate college and spend 30 years at Rocketdyne, a division of the Boeing Company, developing rocket engines and deep space power systems, such as the Space Shuttle Main Engine, his “dream job.” He joined the Hammond board in 2011 and transitioned to CEO in 2013.
This interview, conducted by Paul Crompton, is reprinted from Batteries & Energy Storage Technology (BEST) magazine, with permission from Energy Storage Publishing, copyright 2021. It is published in the U.K. so some words may use the British spelling.

For decades, a lead battery’s critical function was reliably starting an internal combustion engine. Now the technology is being criticised for lacking lithium-ion’s energy density per kilogramme. Terry Murphy, president, CEO and chairman of battery chemical firm Hammond Group, explains why there is still enormous scope for improving lead batteries.
Have you noticed any new trends in the market, and has this informed any shift in the proportions of the products you manufacture over the last five years?
Venture capital and private equity investment has flowed into the lead battery manufacturing and recycling sectors, likely attracted by a stable, non-cyclical business. The new owners are cutting operational costs, but they are also spending money on capital upgrades and are potentially more open to technical changes that can reduce costs or increase performance. Change can bring a fair amount of uncertainty in the workforce, but I think these investors might be more open to innovation in the long run. They also are beginning to realise the enormous potential for growth, especially under a new administration dedicated to renewable energy and infrastructure renewal.
One of the big markets for lead batteries is SLI applications. Tesla is swapping its SLI batteries for lithium-ion. Do you see a significant role for lead-acid batteries outside of SLI in the future?
Lead batteries will remain the dominant technology for SLI. They are cheaper, more tolerant of weather extremes and recyclable. While we see lead batteries remaining the dominant technology for SLI, its greatest potential is for renewable energy storage where, unlike personal electronics and transportation, weight and volume are less of a limiting factor, while sustainability is an absolute must.
How can advances in additives increase SLI lead battery performance, and can lead ever compete with lithium-ion in this market, beyond price?
Lead batteries can be very competitive with lithium-ion, especially at the systems level. Our performance additives have enabled significant advances in cycle life, charge acceptance, and material utilisation. Hybrid configurations with lead batteries are a viable option, whereas lithium-ion applications require steel case protection, thermal management and introduce a significant safety concern, not to mention their lack of sustainability and end-of-life hazard.
You spoke of ‘low hanging fruits’ that need be exploited to boost lead batteries in the last edition of BEST? Can you expand on what you believe these to be?
First, we need to improve utilisation by taking lead out of the battery— that not used in the electrochemical reaction. Bipolar design is a perfect example as it combines the positive and negative plates, thereby reducing lead needed to carry the electrical current. Unique approaches by Gridtential and Advanced Battery Concepts have demonstrated weight savings and other performance improvements.
At Hammond Group we focus on the second part of that equation: increasing active material utilisation through paste additives and enhanced oxides. Our Treated SureCure® provides faster formation, removing an obstacle that had hindered some battery manufacturers from moving to a tetrabasic lead-sulphate cure. This change provides a nominal 5% lead savings as the stronger tetrabasic structure allows a reduction in positive paste density. Our new expander formulations enhance charge acceptance, reduce water loss, and have allowed us to better manage the half-plate potentials to customise blends for the application.
We recently filed a provisional patent on the benefits of lead silicate in the active material to minimise electrolyte stratification and improve cycle life. This novel approach is being evaluated by several battery manufacturers to increase cycle-life performance. Hammond Group is an engineering driven company founded in 1930 to manufacture lead compounds. We are continuing this tradition, investing heavily in R&D to advance the performance of lead-acid batteries.
You’ve spoken of the need for the lead battery industry to embrace innovation, change, and investment. Why did it stop, and how can the industry change its mindset?
I am not sure that innovation ever stopped. I think the focus went to manufacturing efficiencies, increased output, and cost reductions as customers demanded lower prices.
Performance innovation certainly has accelerated over the past few years, as new requirements beyond SLI have emerged. As I mentioned earlier, new investments have been pouring into our sector, bringing both opportunities and challenges. I think the industry recognised the need to address emerging demands from vehicle electrification and energy storage, and continues to make significant strides in improving battery performance to serve these markets.
Do you see opportunities in the ‘green market’?
The green markets are real, especially in backing up the intermittency of renewables. Lithium-ion has been dominant in the recent installations. That choice might have been expedient for the developer, but it is a very bad precedent and needs to be stopped.
A 1,000 lb lithium-ion battery requires 500,000 lbs of earth to be mined and processed and all this material ends up as garbage at the end-of-life. Lead batteries are 99% recyclable, and recyclability must be the overriding requirement when millions of GWh of energy storage are being contemplated.
Lead batteries are made from one element, lead, which is relatively abundant and domestically sourced, whereas the lithium-ion supply chain is reliant on very limited, offshore materials. Lithium-ion should not be used in terrestrial energy storage applications where weight and volume are secondary requirements. Allowing lithium-ion in these applications is a waste of critical materials and mass lithium-ion battery disposal would become our next Yucca Mountain.
What are the biggest challenges for the lead battery industry in the next decade, and how are they being tackled?
Lead’s biggest challenge is its toxic reputation, earned from former, dispersive uses in gasoline, paint, and plumbing. No one wants lead in the ‘environment’. Fortunately, well-established, state-of-the-art recycling and manufacturing systems already in-place, ensure that the lead in batteries remains in batteries.
How has COVID-19 affected overall demand and do you see lead batteries being resilient to market change?
COVID-induced lockdowns affected battery production while demand remained steady. As restrictions were lifted, order books were full and battery producers have been running flat-out to rebuild inventories. Lead batteries have proven, once again, that they are recession-proof and pandemic-proof.
How are the changing needs/demands from lead batteries informing the R&D goals of Hammond?
The future is bright for the battery market as our society demands energy and energy storage. From cell-phones to start/stop cars, to electric cars, to energy storage. Today we have 25GW of energy storage in the USA utility grid, primarily from pumped hydro. That is a fraction of what is needed for the future, as we turn to an electric mobile society.
The question is, where do lead batteries fit in this tremendous market opportunity? I’m bullish on lead batteries. Their recyclability is a huge consideration and the ability to use the same lead over and over in batteries is a game changer.
The need for improved charge acceptance and cycle life has lifted demand for Hammond’s specialty additives, spurred-on negative plate expander formulations and, most recently, inspired a unique approach—using lead mono-silicate in the plates’ active material to inhibit electrolyte acid stratification.
What are your expectations/KPIs for the company over the next 5-10 years?
- Continue with zero OSHA recordable incidents
- Improve the plant air quality by 50%
- Increase battery life by 50%
- Increase charge acceptance by 100%
- Tighten our specifications by 50%
- Reduce our energy requirements by 50%
How can your additives improve the performance of LABs in energy density, cycle life, round trip efficiency and high-rate performance in the next 5-10 years? How far can those improvements go?
It is very application and customer dependent, but we have seen a 100% improvement in cycle life and charge acceptance with several customers. We have developed more than 100 variations of expanders, as each one is tailored to our customer’s application. We know that use of our TTBLS products can lead to a saving of up to 5% in active material while lowering manufacturing costs.
Are you investigating any performance enhancements beyond those mentioned above?
We continue to focus on the fundamental material in the lead battery, the oxide. Hammond specialises in lead oxides and continues to evaluate other forms of oxides that may improve battery performance.
I am excited about our novel work on lead silicate. Conceptually, the lead silicate provides an electrolyte reservoir within the active material to reduce mass transfer to the free electrolyte between the plates. And we can adjust how much electrolyte is stored at each plate to reduce electrolyte stratification. The result is less overcharge needed to mix the electrolyte— therefore less grid corrosion, less active material shedding, improved roundtrip energy efficiency, and longer cycle life. Improving one limitation beneficially touches so many other performance measures.
We are thankful for having amazing customers and see ourselves as an extension of their R&D teams. Understanding their issues and limitations allows us to stay connected with the industry’s needs and maintain a fruitful roadmap. Like our customers, we strive to achieve CBI’s battery performance goals.
Are you looking at any performance enhancing additives other than carbon?
Absolutely. As we better understand the mechanism of carbon in the negative paste, we can make a more informed search for functional alternatives. I am not saying, eliminate the carbon; rather, let’s try to reduce the use of an exotic carbon while achieving similar performance.
Lead silicate has that opportunity as it too impacts the half-cell potentials and, unlike carbon, can be added to both negative and positive plates, allowing us to tailor charge levels at each plate. There is no single, perfect carbon. It is about tailoring additives to provide optimal performance as defined by the desired characteristics. There always will be tradeoffs, yet the days of using one expander for everything are past.
With increased performance criteria in mind, do you foresee Hammond’s development focus likely to be on energy storage as well as, or in place of SLI, in the next decade?
When I look back on our start/stop development work, what we learned for this SLI application later helped us develop better expanders for deep-cycle, UPS, and E-bike applications. Novel advances in improving charge return efficiencies for deep-cycle batteries were an offshoot from knowledge gained when developing EFB program. Innovations for one application often find additional rewards in others and promise to bear fruit in advanced energy storage, which will be a game changer for our industry.
Do you have any plans to diversify into lithium-ion or other battery chemistries as most Pb-A suppliers are doing?
If it makes money! Most recently, the Pb-based nano-composite anode now being investigated for lithium-ion batteries has intrigued us. Our core competence is powdered metallurgy and speciality chemicals. We are focused on lead, but these skills can be brought to bear as the market demands