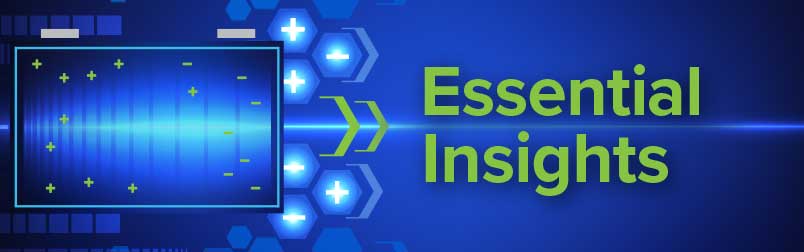
The following post is authored by Jeremy Furr, Senior Vice President of Strategic Sourcing for Stryten Energy, a provider of stored electrical-energy solutions for transportation and industrial markets. Stryten Energy manufactures advanced lead, lithium, and vanadium batteries, as well as intelligent chargers. They also design cloud-based software for smart fleet design decisions. This article was originally published by North American Clean Energy and shared with permission, copyright 2023.
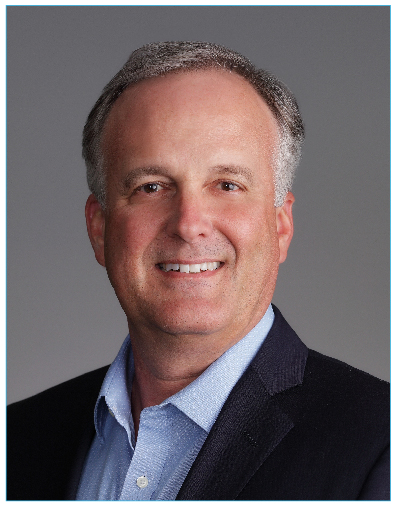
Renewable energy already plays a critical role in U.S. infrastructure. In 2022, it was responsible for 22 percent of domestic energy generation. But the U.S.’s ability to generate clean energy threatens to soon outpace our ability to store the energy these projects generate. The Energy Information Administration estimates that 55 percent of energy generation capacity added this year will come from solar projects. We need a solution that allows us to scale storage projects similarly.
The good news: Congress has given manufacturers the resources needed to enable this long-term storage. The Inflation Reduction Act added more than $60 billion of new funding into clean energy research and infrastructure, including a 30 percent investment tax credit into both standalone and solar-powered storage technology.
The Inflation Reduction Act funding gives us an opportunity to explore more battery chemistries for clean energy storage. But to make real breakthroughs, we need to start with the battery chemistry that’s been the backbone of the industry so far: lead.Lead will continue to be a critical element in our push toward clean energy storage. We should use the lessons learned from the lead battery supply chain to improve the viability of other battery chemistries, such as lithium and vanadium. Here’s how:
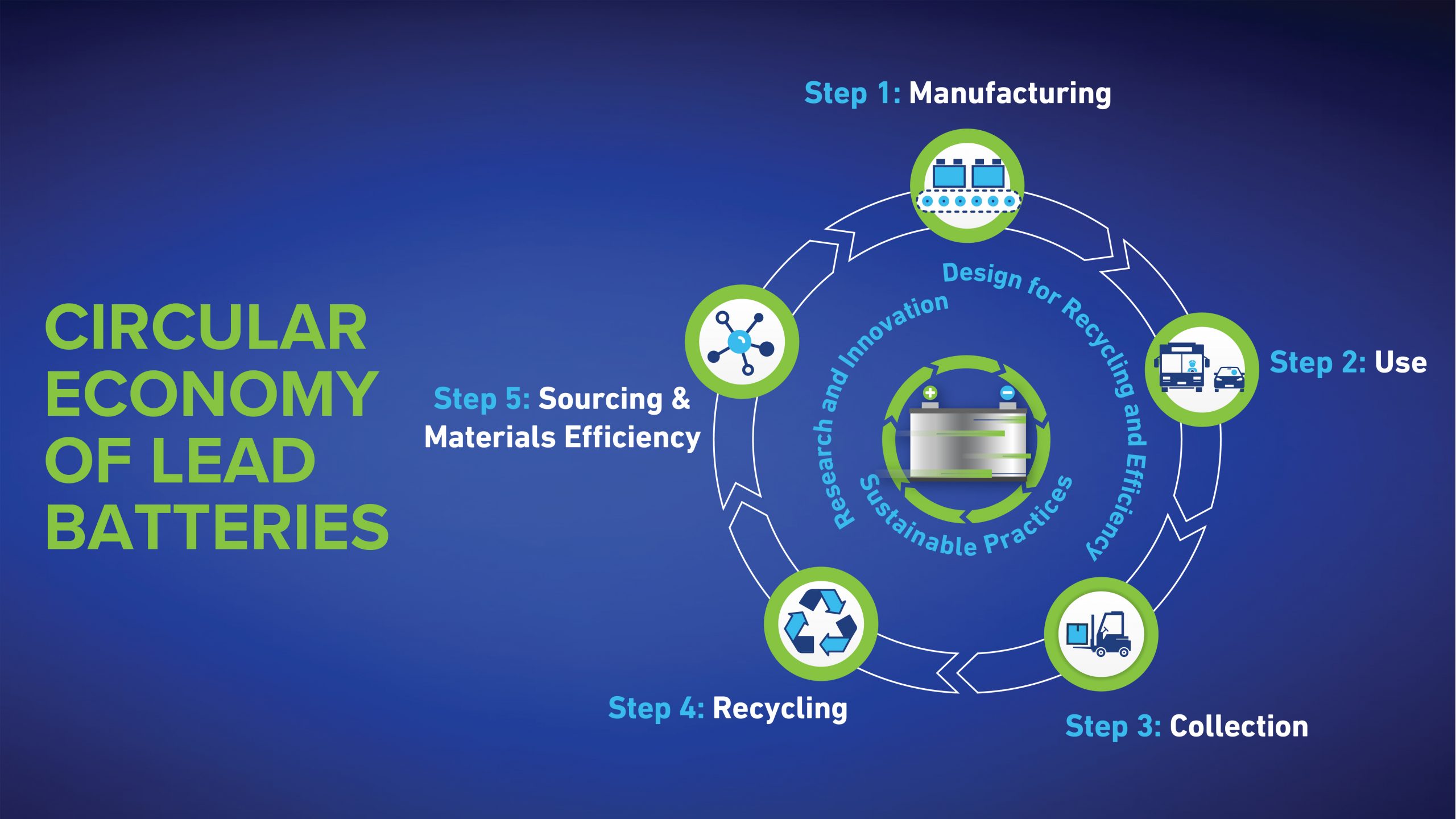
Lead’s Success Story
The secret to lead’s success is its circular economy. Thanks to a well-established network for lead battery recycling, lead batteries in the United States have a recycling rate of almost 100 percent. About 95 percent of a lead battery’s plastic components can also be reused. And, while most recycled products are ultimately refashioned into other materials, spent lead batteries are used to manufacture new lead batteries. In fact, new lead batteries are comprised of approximately 80 percent recycled material. Lead batteries are truly the gold standard of a “cradle to cradle” system.
Lead’s domestic supply chain is another significant benefit for battery manufacturers. The U.S. is the world’s third-largest lead mining country, with an estimated 280,000 metric tons of recoverable lead produced state-side in 2022. In the same year, approximately 950,000 metric tons of lead were recycled in the United States. While lead’s recyclability means U.S. battery manufacturers aren’t required to tap much of this new supply, this surplus of materials is quite beneficial from a sustainability perspective.
The combination of high recyclability and domestic supply chain means that lead batteries make a significantly smaller impact on our environment, all while simplifying manufacturing and reducing costs. That’s the approach we need to examine for other battery chemistries.
Other Chemistries
As demand for materials to power clean energy solutions has risen, lithium had a first-to-market advantage for higher power density energy storage. While it may be a viable solution for some applications, it has far to go to claim as sustainable a footprint as lead.
To make lithium viable, we’ll first need to consider its supply chain. Unlike its lead supply, the U.S. lacks a rich deposit of lithium. As a result, manufacturers are required to look outside of the U.S., leaving them vulnerable to shipping delays and geopolitical tensions. Battery manufacturers using lithium for energy storage solutions must also compete with manufacturers building batteries for electric vehicles, as well as other consumer products.
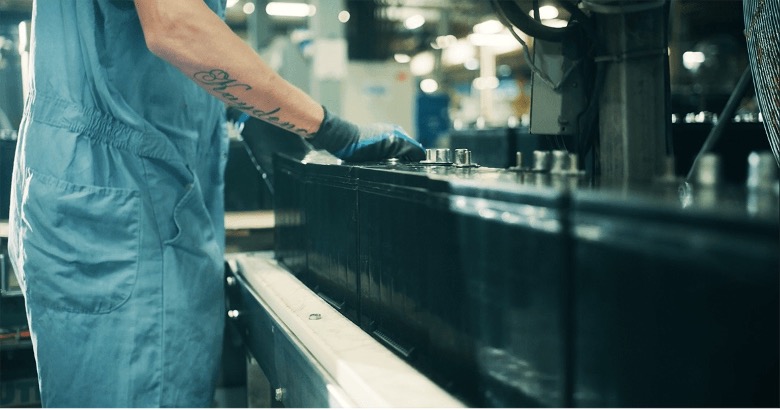
Another challenge is lithium recycling. Only about 5 percent of used lithium batteries are recycled, necessitating heavy mining investments, and hindering sustainability efforts. The Environmental Protection Agency is developing best practices to increase lithium’s recyclability, based on feedback from various industries connected to the battery recycling process. As lithium demand increases, recycling will become critical.
Another battery chemistry that has potential to more closely reflect the lead supply chain is vanadium. Although the technology is still young, vanadium redox flow batteries (VRFB) have shown promise. One major benefit is a near-infinite cycle life (with proper maintenance). VRFB systems offer stable storage capacity for 20-30 years. With such a long lifespan, these battery systems use a more sustainable energy storage technology. The electrolyte that constitutes the bulk of a VRFB system is almost infinitely reusable, meaning we can drive the batteries through a recycling supply chain similar to that of lead. As manufacturers take advantage of Inflation Reduction Act provisions, one of the first priorities should be to make vanadium viable at a larger scale, and develop a domestic supply chain for its battery components.
A Trio of Solutions
Building the U.S. energy infrastructure to transition to clean energy long-term is a big challenge, and big challenges call for bold solutions. The lead battery supply chain is also a blueprint for what should be next for all chemistries.
By innovating new ways to recycle lithium, investing in new facilities to manufacture and assemble lithium batteries, and capitalizing on vanadium’s recyclable properties, we can transform these materials into viable options for storing renewable energy alongside lead — and fully leverage the power of renewable energy generation.
Additional articles by Jeremy Furr: