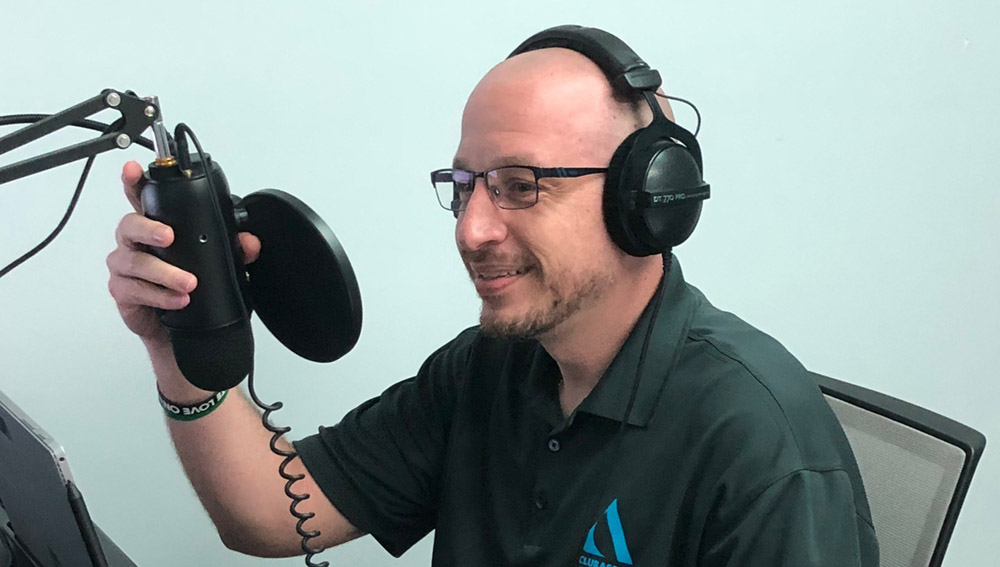
This is the second of our three-part blog series during this important week.
As we continue our celebration of Safe + Sound Week August 13 – 19, we’re broadening our definition of “safe.” Lead battery manufacturers, recyclers and suppliers not only protect their employees, but their communities and the environment, too.
In fact, the lead battery industry is one of the most highly regulated industries in the U.S. and is subject to strict air and water release limits to protect human health. Innovation in manufacturing is further reducing environmental impact, while revolutionizing worker safety and efficiencies.
Speaking of efficiencies, lead batteries are recycled at the highest recycling rate of all consumer products – 99.3 percent. From design through recycling and re-use, the circular economy of lead batteries greatly reduces their environmental footprint. The modern, closed-loop recycling process keeps more than 122 million lead batteries from landfills each year.
Environmental Stewardship in Action
All facilities where lead batteries are recycled or manufactured continually monitor the surrounding air for emissions, as required by the Environmental Protection Agency. California lead battery recycler Quemetco invested more than $25 million for the installation and maintenance of a state-of-the-art environmental control system and monitoring devices. Quemetco’s two U.S. sister recycling facilities subsequently invested more than $70 million in the same Wet Electrostatic Precipitator (WESP) technology. Today, stack emissions of lead at each is less than the emissions from one 1950s Chevrolet.
This is one example of numerous technologies that make air emissions from lead battery production and recycling less than one percent of total U.S. lead emissions.
Safe Workplaces Lead to Broader Benefits
“When we start with the understanding that we must first work safely, we can then expect other positive outcomes to follow,” says Anthony Staley, general manager of The Doe Run Company’s Buick Resource Recycling facility located in Boss, Mo. His team starts each shift with a safety contact to help keep the focus on working safely and watching out for one another. And it’s working.
The company’s mining operations have received the National Mining Association’s prestigious Sentinels of Safety Award 28 times since 1971 for excellence in mining safety. Recently, the company’s wholly owned subsidiary, Fabricated Products Inc., achieved 18 years without a lost-time accident at both its FPI facility in Washington and Seafab Metals facility in Arizona. And this year, the company’s Southeast Missouri Port achieved 12 years with no lost time accidents.
Gopher Resource, an Eagan, Minn., based lead battery recycler makes “safety first” one of its five core commitments and invests more than 15,000 hours annually for safety training. The company extends that mindful thinking into the communities where it operates by monitoring livability concerns, like operational hours, truck routing, sound, facility landscaping and practicing community connection in tangible ways. This is in addition to maintaining modern safety equipment and systematic processes that create valuable new products from spent lead batteries.
Fostering Safety with Fun and Technology?
Yes! During Safe + Sound Week, Doe Run’s safety committee will roll out a competition titled, “Safe & Sound September SLAM,” (Stop, Look, Analyze and Manage). It will encourage employees to pause, look for potential hazards, analyze the best way to address them, and manage the potential hazards to eliminate or minimize them. Awards will go to the top three SLAM situations submitted.
Club Assist North America has made its safety programs more interactive. The company is known for its mobile automotive services in battery supply and replacement and glass repair and replacement. To reach its 200-plus geographically dispersed workforce, the company’s safety manager launched a podcast that employees can download and listen to when and where convenient. Company statistics show employees are listening to the entire thing.
Don’t Miss Our First Safe + Sound Blog Post
You can access “Safe + Sound Week: Employee Safety” here .