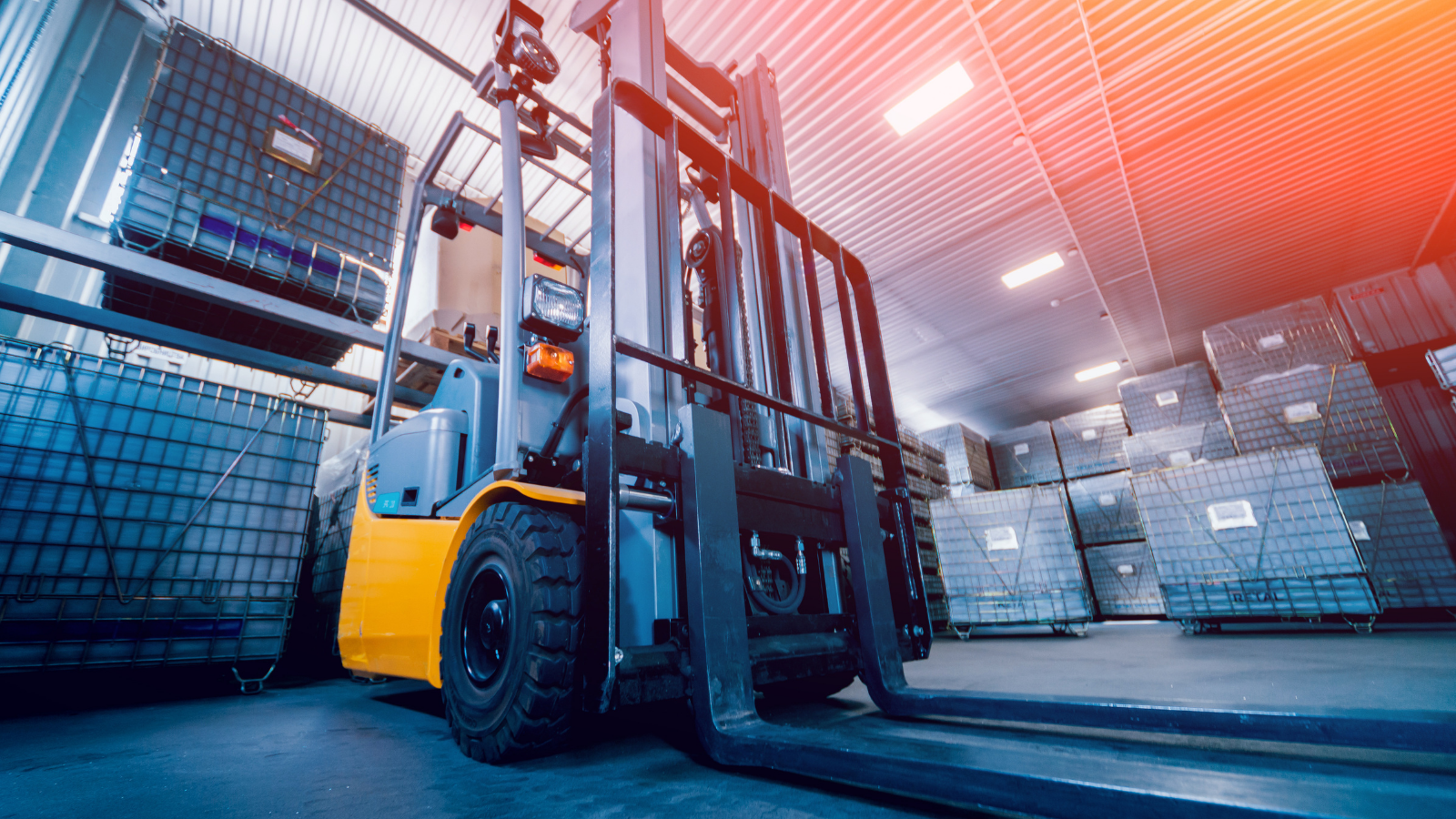
Forklifts have long been the reliable workhorses in moving materials from point A to point B. Now, electric forklifts – and the lead batteries that power them – are becoming major players in the booming post-pandemic economic recovery that’s underway.
Forklifts are considered industrial trucks and are classified as “motive power.” An amazing 90% of motive power battery demand is met by lead batteries. As new construction surges, these zero-emission forklifts will do the heavy lifting, transferring essential materials from warehouses to workers.
Economy to Surpass Pre-Pandemic Levels
How big is the boom? “It’s unlike anything you’ve seen,” according to the Wall Street Journal.
Analysts project the economy’s size to surpass pre-pandemic levels. By year-end, gross domestic product will rank as if the pandemic never happened. Adding juice to the recovery is an expected infrastructure wave with plans to rebuild airports, rail networks and power plants.
“As the economy continues to quickly rebound from pandemic levels, there is a formidable challenge to strengthen the supply chain with a clean and sustainable source of battery power,” said Jim Rubright, vice president, Motive Power Sales, East Penn Manufacturing, in Lyons Station, Penn.
All of this will further up the demand for forklifts, which is driving the nearly 8% growth in global motive battery demand through 2030. Today, forklifts are a nearly $50 billion industry essential to e-commerce, retail sectors, warehousing and logistics, and industrialization in emerging markets.
Electric Forklifts vs. Internal Combustion (IC) Forklifts
There are many benefits to using electric rather than IC forklifts. The primary difference between the two is that electric forklifts operate on a battery, rather than fossil fuels such as diesel, gasoline or liquid propane gas.
That distinction is helping electric forklifts to rapidly gain popularity in developed nations. Operators can get the job done, but with added health and safety bonuses, especially when working indoors:
- No need to store engine fuel on site
- Cleaner air and reduced noise pollution for workers
- Zero emissions to support cleaner goods and food processing areas
Lead Batteries: An Essential Resource to Achieve Zero-Emission Energy Goals
The use of lead battery technology for electric forklifts and other clean energy applications is also critical for helping industry sectors and policymakers achieve zero-emission energy mandates, and most importantly, curb climate change.
Rubright noted that “Lead batteries continue to help support carbon reduction initiatives while providing this critical, domestically-sourced power to our nationwide forklift fleet.”
For example, the logistics and transport sector accounts for around 2.8 billion tons of equivalent carbon dioxide, which is about 5.5% of total greenhouse gas emissions annually in the U.S. A comparable fleet of electric forklifts will use 83.5% less CO2 than its IC counterpart. And, there’s no need for engine, transmission or coolant fluid changes.
Furthermore, electric forklifts powered by lead batteries are part of a true circular economy, using recycled lead, electrolyte and plastic casings to manufacture new batteries. Lead batteries, including those in forklifts, are the most recycled product in the U.S., according to the Environmental Protection Agency.
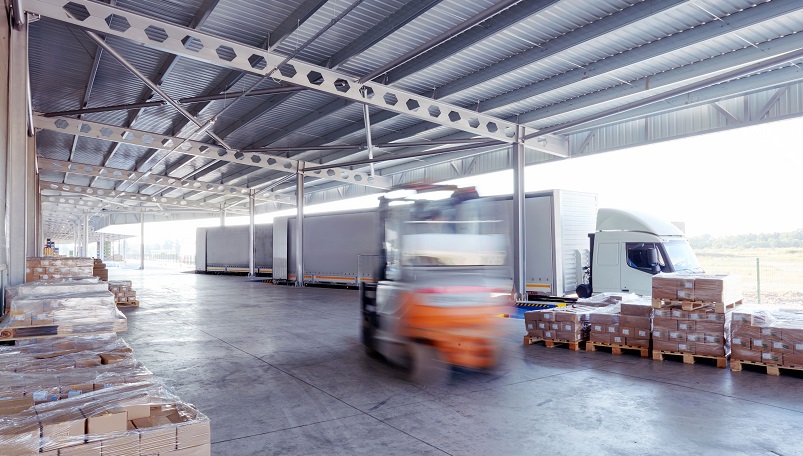
Lead Battery Electric Forklifts Have Lower Total Cost of Ownership
The cost to operate lead battery electric forklifts over the equipment lifetime is part of the consideration in making buying decisions. Lead batteries have demonstrated that they provide a lower Total Cost of Ownership (TCO) when comparing these factors to other battery chemistries like lithium-ion and hydrogen:
- Initial cost of purchase
- Energy efficiency (how long the forklift can run on one battery charge or one tank of fuel)
- Cost of fuel or electricity
- Cost of maintaining air quality in a warehouse
- Cost to maintain the forklift, including batteries (IC forklifts also have batteries), fluids, tires, filters
- Opportunity cost of infrastructure to accommodate refueling, battery charging stations, etc.
- Reliability (e.g., work time lost due to forklift scheduled down-time)
- Cost vs. credit for end of life of the battery
Innovations in electric forklift technology have shown that modern electric forklifts can replace IC forklifts in every application with no loss in performance. A TCO analysis shows that electric forklifts are the more efficient technology.
Ready to Meet Market Demand with U.S. Lead Battery Infrastructure
Lead batteries have additional unique attributes, beyond providing safe and reliable power for electric forklifts with minimal-to-no environmental impact.
Lead batteries are a U.S. manufacturing success and boast a robust, ready-to-scale infrastructure with their existing manufacturing, collection and recycling footprint. This closed-loop supply chain ensures feedstock for new lead batteries remains available and protected from global disruptions in the supply chain.
Put simply, unlike lithium batteries, lead batteries do not rely on imported critical materials or specialty materials. Approximately 90% of North American lead battery demand is met by North American battery manufacturers. Moreover, lead batteries possess high load bearing capacity and high discharge rate, which, in turn, acts as the driving factors in the growth of the lead forklift battery market in the U.S.
From the Warehouse to Your House
More than ever, zero-emission electric forklifts powered by lead batteries are working behind the scenes to keep our economy moving and booming. Knowing that they are also helping to meet our sustainability goals is an added bonus. Says Rubright, “They are a smart choice to keep us moving forward.”