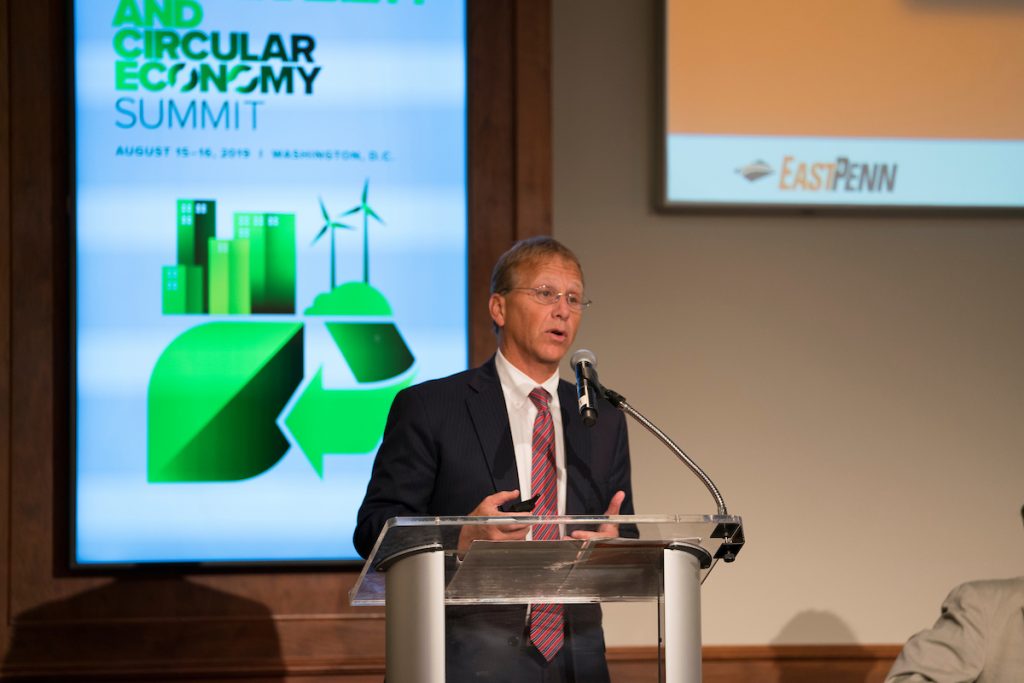
August 22, 2019
The component list for a lead battery is short: lead, plastic and acid. This simplicity is a significant part of what makes lead batteries a circular manufacturing superstar. Better yet, that’s true, whether for a 6-pound battery on a motorcycle or a 50,000-pound pack of batteries for a locomotive.
Lead battery manufacturing and recycling industry executives delivered that message at the U.S. Chamber of Commerce Foundation’s 5th Annual Sustainability and Circular Economy Summit held August 15–16 in Washington, D.C. During a session titled “Data for Good,” battery and sustainability experts discussed the circular economy of lead batteries and how the industry’s successful model can serve as an example for other industries and battery chemistries.
Sharing Circularity Stories
To further share “Data for Good,” this blog and our next will highlight circular success stories given by industry panelists during the session. We’re featuring East Penn Manufacturing (this blog) and RSR Technologies (up next). Both companies are prominent lead battery manufacturers and recyclers who have collaborated with the Department of Energy’s Argonne National Laboratory on research to further improve the performance of innovative lead batteries.
“The right thing to do.”
Chris Pruitt is CEO and President of East Penn Manufacturing Co., Inc., in Berks County, Pennsylvania. He said the idea to recycle, reuse and remanufacture materials is as true today as it was more than 70 years ago, because “our founder thought it was the right thing to do.”
That forward-thinking philosophy is having a huge impact. When East Penn was founded in 1946, the goal was to manufacture 100 batteries a day. Today, in a classic American success story, the firm manufactures 160,000 batteries daily. Each new battery typically consists of 80%+ recycled-battery material. Lead batteries are the most recycled consumer product in North America, with a 99.3% recycling rate. Plus, lead is a metal that can be recycled infinitely without losing its valuable properties.
Big Benefits Make It Work
Pruitt said the substantial economic and sustainability benefits of circularity make the system work for East Penn, which recycles a battery’s lead, plastic and acid all on-site. He gave this example: “On a Monday, a customer gives us a battery back that’s been used; it no longer has life. By the next Monday, that battery is new … with 80% of it made from recycled material.” Through East Penn’s own distribution system, it collects spent batteries and processes them to separate the lead, plastic and acid.
In addition to recycling the lead, the company has equipment to recycle 60 million pounds of plastic annually. “It [a plastic battery case] is ground into pellets, then is automatically conveyed into our Injection Molding facility.” Within a week, a battery’s materials have been remanufactured to create a new battery that is ready to ship. The closed-loop process then repeats: use-recycle-remanufacture-redistribute.
Creating Byproducts, New Markets
In the spirit of a true circular economy, East Penn also uses reclaimed battery materials to create products for other markets. The company has recycled more than 50,000 tons of 92% sulfuric acid since 2000. Each year, East Penn produces 25,000 tons of liquid fertilizer for farmers in the local area and along the East Coast. Another byproduct is sodium sulfate (used by the garment and dye industry), which comes from the industrial water in the company’s wastewater facility.
Speaking of water, the company doesn’t discharge any wastewater from its facility. Instead, it saves 100,000 gallons per day to be reused in the manufacturing process.
Stay tuned: Check back for the third part in this blog series on the 2019 Sustainability and Circular Economy Summit. RSR Technologies will share what new battery chemistries can learn from the science behind the lead battery industry’s success in circular manufacturing.
Learn More
InsideEPA.com: Lead Batteries’ Top Sustainability Score May Be Model For Other Sectors
News Release: Lead Batteries A Model of Circular Economy at D.C. Sustainability Summit
East Penn Manufacturing
RSR Technologies
The Sustainability Consortium
Chamber of Commerce Foundation 5th Annual Sustainability and Circular Economy Summit