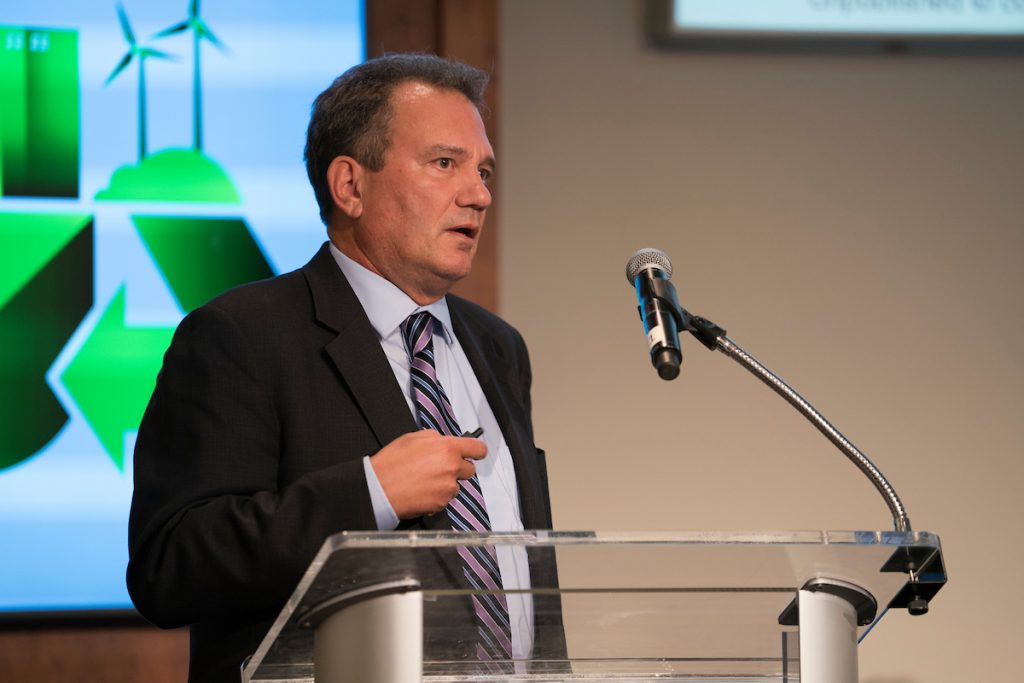
August 29, 2019
As the planet warms and governments create mandates for decarbonization, the lead battery industry – with its closed-loop circular economy — is doing its part to contribute to sustainability. What’s preventing new battery chemistries from doing the same?
The question was one of many answered during the U.S. Chamber of Commerce Foundation’s 5th Annual Sustainability and Circular Economy Summit held August 15–16 in Washington, D.C. This blog is part three in our series highlighting the Summit session titled “Data for Good.” It united top battery and sustainability experts to discuss the circular economy of lead batteries and how the industry can model circularity for other industries and new battery chemistries.
RSR Technologies Shares Science Insights
Following an overview presentation on the lead battery manufacturing and recycling industry, Dr. Mark Drezdzon guided Summit attendees deeper into the recycling process. He is Vice President of Research and Development at RSR Technologies, a subsidiary of ECOBAT Technologies, one of the largest recyclers and manufacturers of lead on the planet.
“We [RSR] don’t manufacture batteries. Our product is lead. What I’m here to talk about today … is how that’s done from a scientific standpoint and maybe some of the lessons that can be learned for other recyclable products on how to develop these processes,” Drezdzon said.
A chemist by training, Drezdzon continued, “I’ve played with every element in the periodic table. So I know the fascination of dealing with some of these new technologies [lithium-ion] and it’s so new, that there’s still a lot to learn about how we move forward with things like a circular economy for these types of advanced batteries.”
Battery Recyclability: Lead vs. Lithium-Ion
Drezdzon described the many technical challenges to recycle lithium-ion batteries, which currently follow a linear manufacturing model of take-make-dispose, with a less than 5% recycling rate. Lead batteries have a 99.3% recycling rate.
Here is some of what accounts for the recycling chasm between the two chemistries:
MATERIALS
- Lead Battery: Drezdzon stated that a lead battery has “a relatively simple recycling process.” A fairly standard chemistry (lead, plastic and sulfuric acid) creates uniformity, regardless of the battery manufacturer. (A universal fact of recycling is that the less diverse the materials and chemistries, the easier to sort.)
Drezdzon said the variety of shapes and sizes of lead batteries is also irrelevant. This makes lead batteries well-suited for high-throughput processing. “Our scrap battery crushing rate is around 60 short tons per hour. That’s a lot of mass to put through a system in one hour. For refined lead and lead alloy production, we can make about 300 short tons per day of material to go back to somebody to make new batteries.”
- Lithium-Ion Battery: The complexity and variety of materials make it difficult to put lithium-ion batteries into a recycling loop, Drezdzon stated. He showed a picture of a Chevy Volt battery and said, “These things are really fascinating. They’re very complex in that they have to be robust; they have to withstand anything that might happen out on the road. But they’ve got so many materials involved with them that are actually not involved with the battery in the first place.”
As examples, he listed the battery’s steel outer shell casing and the electronic components that control the battery cell health, and concluded, “What you really have is a battery and all this structure around it to protect it and a computer to run it.”
STATE OF CHARGE
- Lead Battery: Regarding safety during recycling, Drezdzon explained that for lead batteries, their state-of-charge when reclaimed isn’t important. “Most lead batteries received for recycling are spent, but if a fully charged battery arrives, it doesn’t matter.”
- Lithium-Ion Battery: Unlike a lead battery where the state of charge is irrelevant, “The state of charge is important, because if you don’t take these apart safely, you can knock yourself into next week real easy. You have to make sure that they’re discharged properly so you don’t injure yourself.”
ELECTROLYTE CHEMISTRY
- Lead Battery: A lead battery uses sulfuric acid, which is non-volatile and relatively easy to handle with appropriate equipment and personnel protection.
- Lithium-Ion Battery: “Lithium-ion batteries use low-boiling-point organics which are subject to potential fire and explosions and must be handled very carefully.” The fact that there is no standard chemistry for a lithium-ion chemistry, literally more than a dozen are in use, also makes it challenging for sorting and recycling. And finally, there’s a safety risk when the lithium-ion batteries begin to fail and have the potential become over-pressurized and explode.”
Design to Recycle
According to Drezdzon, “The key point is that we need to educate the population that all batteries are not created equal.” He compared the battery industry to the plastics industry where there are many different types of plastics, which contributes to the problem of plastic waste.
“With today’s lithium-ion batteries, the recycling challenge is that there are so many different types of batteries, you must first isolate the cell material, remove binder that keeps it together, and then deal with the many different chemistries.”
Drezdzon posed a thought. “The question is: Is there someday going to be a single standard for the chemistry in lithium batteries? It would make recycling the batteries much easier, and it also would allow [the lithium-ion] industry to do the same thing that the lead industry is doing. This would allow somebody who does the recycling to generate a product that someone is willing to buy as a secondary product to make new lithium batteries.”
He added, “When you come up with a way to improve the performance of the battery without affecting its recyclability, that is a very big thing.” The bottom line, Drezdzon concluded, “We need to design products that can be recycled; it’s real easy to design some that can’t.”
Lead Research-In-Progress
Drezdzon explained how research is uncovering new knowledge about lead. Historically, battery manufacturers have tried to make lead purer to improve performance. This led to the advent of maintenance-free batteries, which don’t need water added weekly, as they did in the last century. But researchers found that as the lead became purer, it reached a point where there was a diminishing return on performance. They sometimes removed something in the lead that actually helped the battery performance.
This recognition was the impetus to form a collective industry effort to use high tech tools to better understand lead properties. RSR Technologies is involved in that project because, “We’re don’t make batteries, but we are in the business of improving lead to make a better-performing battery.”
He cited research being conducted at the Department of Energy’s Argonne National Laboratory with the Advanced Photon Synchrotron (APS) to study lead battery chemistry at the molecular level. The APS, a high-energy X-ray source, looks at what happens when a battery charges and discharges. So far, they’ve learned that if you make the lead just a little different, you get a totally different structure, which performs almost twice as well.
“The fun stuff has just started. We’re looking at the real time charge and discharge of a lead plate with the APS. We are starting to learn how a lead battery operates 160 years after the first one was invented,” Drezdzon concluded.
Lead Battery Innovation Ahead
Essential Energy Everyday promises to keep you posted on all of the new discoveries ahead for innovative lead batteries, an inspiring model for a closed-loop circular economy.
Learn More
InsideEPA.com: Lead Batteries’ Top Sustainability Score May Be Model For Other Sectors
News Release: Lead Batteries A Model of Circular Economy at D.C. Sustainability Summit
East Penn Manufacturing
RSR Technologies
The Sustainability Consortium
News Release: Battery Mainstay Headed for High-Tech Makeover