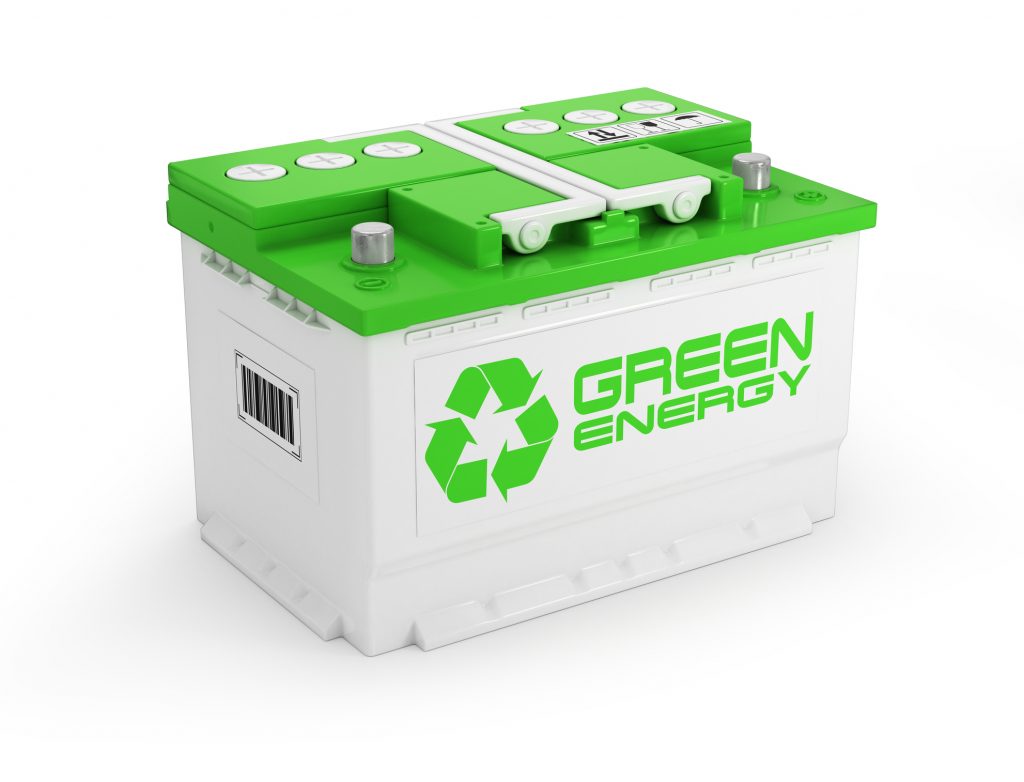
“Reduce, Reuse, Recycle,” are three words the lead battery industry never tires of hearing. Though we just celebrated Global Recycling Day in March, we’re happy to join countries around the world to promote International Recycling Day on May 17.
Lead Batteries Rank #1 in Recycling
Here’s the backstory on why lead batteries are so well suited to protect the planet and preserve our natural resources.
Lead batteries are primarily comprised of three materials: lead, sulfuric acid and plastic. Each are recycled, making the manufacture of lead batteries a great example of a circular economy. In fact, a recent study by Battery Council International, and confirmed by the Environmental Protection agency, reports that, with a recycling rate of 99.3 percent, lead batteries are the most recycled consumer product in the U.S.
Lead: Its Two Origins
Where does lead come from? According to the International Lead Association (ILA), as with all metals, there are two main production routes. Primary production from mined lead ore is the original source of all lead. Secondary production is where lead is recovered from recycled products or from residues arising from the production process. The latter is what makes lead batteries such a great example of sustainability.
Secondary lead production now accounts for more than half of all lead produced throughout the world. In the U.S., more than 80 percent of lead comes from secondary production, and every new lead battery consists of up to 80 percent recycled lead – it’s infinitely recyclable. Let’s take a closer look at how the process works.
The Lead Battery Recycling Process
This is how our industry takes materials that would be discarded and turns them into useful products.
When a spent battery is returned to the plant, it’s broken apart in a hammer mill (a machine that breaks the battery into pieces). The pieces go into a vat where the lead and heavy materials fall to the bottom, while the plastic rises to the top. Those plastic (polypropylene) pieces are scooped away and the liquids are drawn off, leaving the lead and heavy metals. Each of the materials then begins its recycling journey:
Plastic. The polypropylene pieces are washed, dried, and sent to a plastic recycler where the pieces are melted together into an almost-liquid state. The molten plastic is put through an extruder that produces small plastic pellets of a uniform size. Those pellets are sold to the manufacturer of battery cases, and the process begins again.
Lead. The lead grids, lead oxide and other lead parts are cleaned and then melted together in smelting furnaces. The molten lead is poured into ingot molds. After a few minutes, the impurities, otherwise known as “dross,” float to the top of the still-molten lead in the ingot molds. The dross is scraped away, and the ingots are left to cool.
When the ingots are cool, they are removed from the molds and sent to battery manufacturers. The ingots are then re-melted and used in the production of new lead plates and other parts for new batteries.
Sulfuric acid. Used battery acid can be handled in two ways. The acid is neutralized with an industrial compound similar to household baking soda. This turns the acid into water. The water is treated, cleaned and tested to ensure it meets strict clean-water standards. Then it’s released into the public sewer system.
Another way to treat acid is to process it and convert it to sodium sulfate, an odorless white powder that is used in laundry detergent, glass and textile manufacturing. Acid can also be reclaimed and reused in new battery products through innovative recycling processes.
A Sustainability Success Story
This completes the state-of-the-art “closed loop” process that keeps more than 1.7 million tons of lead batteries out of U.S. landfills annually. It’s a first-class story of sustainability drawn from the second, and third and fourth to infinity reuses of the lead battery.
Thank you to everyone who plays a role in making lead batteries a sustainability superstar. It’s a wonderful way to celebrate International Recycling Day 2018!
(Special thanks to Battery Council International and International Lead Association for providing background information.)
Learn More
- Watch our Good Neighbors Video
- Lead Battery Recycling
- BCI National Recycling Rate Study
- America’s Most Recycled Product Infographic
- Global Recycling Day blog